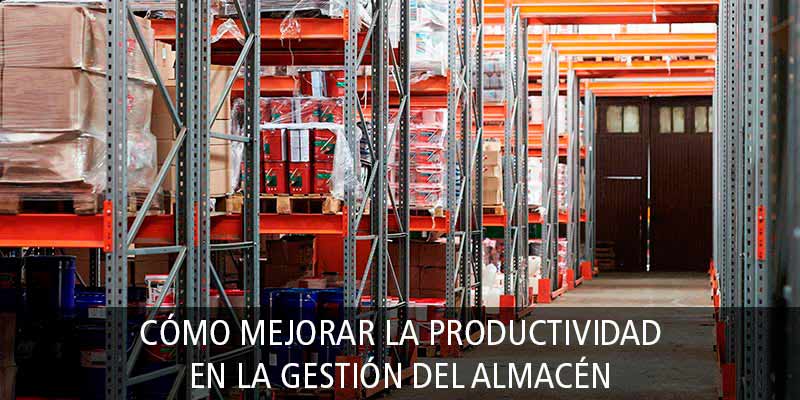
En realidad, mejorar la productividad en un almacén se parece bastante a mejorarla en cualquier otro entorno. Al final, se trata simple y llanamente de hacer más con menos, es decir, de sacar el máximo rendimiento al almacén con el mínimo consumo de recursos posible. Si sustituimos la palabra “almacén” por “fábrica”, “proceso”, “área”, “producto”, “producción” o por el término que deseemos veremos que, colocando el artículo adecuado por aquello de la concordancia, encaja perfectamente.
Cuando hablamos de productividad podemos hablar simplemente de una relación entre entradas y salidas. Para producción, los conceptos y parámetros que debemos colocar para referirnos a esas entradas y salidas serán diferentes (algunos coinciden) que para almacén, pero la relación existente entre ellas es la misma.
En un almacén se emplea maquinaria, mano de obra, materiales, una determinada metodología que tendrá cierto impacto sobre el medio ambiente para ofrecer un servicio y en ocasiones para realizar pequeñas transformaciones de producto. Todas estas entradas, sean de la índole que sean, pueden traducirse en dinero, en coste. Por supuesto que los logísticos no somos una excepción en este mundo empresarial y, por tanto, dentro del almacén todas esas entradas se combinarán con los diferentes procesos y como resultado generarán salidas, referencias servidas, el costo asociado, la calidad del servicio, tiempos de ejecución, tiempos muertos, incidencias, etc.
Simplificando mucho podemos entender que si en un período concreto, para servir 1000 unidades hemos tenido un costo de 1000€, nuestra productividad es de 1 unidad servida/€. Si en un período posterior hemos aplicado una serie de mejoras y hemos logrado reducir los costos por ejemplo a 100€, veremos que nuestra productividad aumenta hasta las 10ud./€ sin aumentar el número de piezas servidas por período. Si nos fijamos en este supuesto simplón, eran los desperdicios los que estaban limitando enormemente nuestra productividad en el almacén. La gran ventaja es que en la mayoría de las ocasiones veremos que, estos desperdicios improductivos, están sujetos a nuestro control, es decir, que podremos actuar sobre ellos con relativa facilidad.
No es la única causa de improductividad, pero en un almacén, a medida que aumenta la velocidad de transmisión y la precisión del flujo de información, aumenta la productividad de forma vertiginosa. Es lógico pues el ritmo de trabajo tiene mucho que ver con el ritmo al que la información fluye. Pensemos en el tiempo que empleamos en servir un único pedido en papel (flujo de información lento) o a través de una PDA (flujo de información inmediato). Se aprecia enseguida fijándonos únicamente en el tiempo de espera del operario desde que el pedido se conforma hasta que lo recibe impreso en la mano frente al la inexistencia total de espera usando una PDA, y no es el único tiempo muerto del proceso manual.
Con una adecuada gestión del almacén centramos nuestros esfuerzos en mejorar aquello que verdaderamente podemos controlar, es decir, nuestros procesos. Controlándolos y mejorándolos podremos mejorar la productividad de cada uno de ellos y en conjunto la del almacén.
Cuando hablamos de gestión de almacén adecuada hablamos de gestión enfocada a eliminar desperdicios o despilfarros, es decir, todo aquello que no aporta valor, pero sí genera costes. Esto es válido tanto para la recepción, el almacenaje y la expedición de materiales.
Eliminar desperdicios implica identificarlos previamente, es decir, medir, manejar indicadores, transformarlos en información y hacer buen uso de ella. De manera que identificando esas “no aportaciones de valor” y eliminándolas o reduciéndolas podemos emprender acciones de mejora en cada una de esas áreas. manteniendo siempre el objetivo de mejorar la productividad. De forma general debemos atacar a todo aquello que suponga una pérdida de tiempo ya sea por una mala planificación, ejecución o error.
La primera medida que cualquier empresa debe tomar para mejorar la productividad en el almacén sin duda alguna es implementar un buen sistema SGA que gestione eficientemente cada proceso, pero no es la única medida.
Acciones que se pueden tomar para mejorar la productividad del almacén
En la recepción de materiales.
La recepción de mercancías es un proceso complejo que abarca multitud de tareas administrativas y operativas. El proceso de recepción se compone de acciones previas a la llegada de la mercancía, acciones que se ejecutan a la llegada y otras que se desempeñan tras la llegada de la misma. Además, tiene un componente necesario, inevitable pero difícil de controlar que es el proveedor y sus circunstancias.
Pero precisamente por eso las oportunidades de mejora son muy numerosas y podemos actuar de multitud de formas para mejorar la productividad en la recepción. Por poner algunos ejemplos aquí podremos identificar algunas causas de despilfarro frecuentes como son los errores de clasificación, comunicaciones nada ágiles, falta de medios, procesos duplicados por falta de fiabilidad, etc.
En el almacenaje de materiales.
Entre la recepción y la expedición se sitúa el almacenaje de mercancías. Parece mentira que tan sólo en el hecho de mantener una serie de mercancías en sus ubicaciones, haya que tener en cuenta la gran cantidad de factores que se deben gestionar, pero así es. Eso representa desde un enfoque productivo de buena gestión, una gran cantidad de oportunidades de mejora de la productividad del almacén.
Entre estos factores que podemos mejorar y gestionar están el espacio disponible, los movimientos de las mercancías, su rotación, su ubicación, los sistemas de control, etc. Pero, además, dentro de esta categoría vamos a incluir las acciones de inventario, es decir de recuento de las existencias.
Todos esos factores afectan positiva o negativamente a la productividad del almacén y deben ser medidos y tratados adecuadamente.
En la expedición de materiales.
La expedición es la culminación de nuestra labor logística en el almacén y donde nos jugamos el todo por el todo. Normalmente en esta fase se emplea gran cantidad de mano de obra, pero no necesariamente con los recursos adecuados por lo que tiene una clara tendencia a convertirse en el cuello de botella de la cadena logística y de suministro. En este proceso de expedición tenemos movimientos de personas, de mercancías, de elementos auxiliares, cambios de unidad de carga, agrupaciones, desagrupaciones, etc.
Desde la preparación de pedidos hasta la expedición de éstos, tenemos mucha variedad de acciones como la selección y recogida de existencias (picking), combinación si procede, consolidación, acondicionamiento y por supuesto la propia carga de los pedidos terminados.
Un alto porcentaje de los costes operativos de almacén se concentran aquí, así que inevitablemente será un foco de atención y de acciones de mejora.
Conclusiones
Sin duda un sistema SGA ayuda a mejorar enormemente la gestión del almacén, pero no es lo único que tenemos a nuestro alcance para realizar mejoras. Reducir desperdicios al tiempo que aumenta el valor es un objetivo que puede abordarse también desde la perspectiva del Lean Manufacturing. Tecnología y Lean van de la mano ya que sus objetivos no sólo son paralelos, sino que en ocasiones son idénticos.
Cualquier proceso consume recursos, materiales, utiliza personas, tiempo y dinero y su eficacia se mide por los indicadores de su productividad. Alcanzar niveles óptimos de productividad no es una tarea sencilla y requiere planificación, información y método. A veces basta con reducir la variabilidad de un proceso para mejorarlo, otras eliminar sobrecargas de recursos o sobreesfuerzos que impiden rendir al máximo. En otras, basta con invertir en los medios adecuados. Podemos clavar un clavo con una llave inglesa pero indudablemente con un martillo lo haremos mucho más rápido, mejor y en menos tiempo, además liberaremos la llave inglesa para que pueda usarse para lo que se diseñó, que es en lo que realmente aporta valor. Doble mejora.
Al final todo se reduce a emplear recursos y acciones que aumenten el valor minimizando los desperdicios. En un almacén los más frecuentes (no los únicos) son los tiempos muertos y los desplazamientos de todo tipo.
En esta serie de post dedicados a la productividad en el almacén trataremos de identificar los desperdicios más comunes en la gestión del almacén para poder emprender acciones que traigan consigo mejoras productivas.
*Foto de Tiger Lily en Pexels
También te pueden interesar...