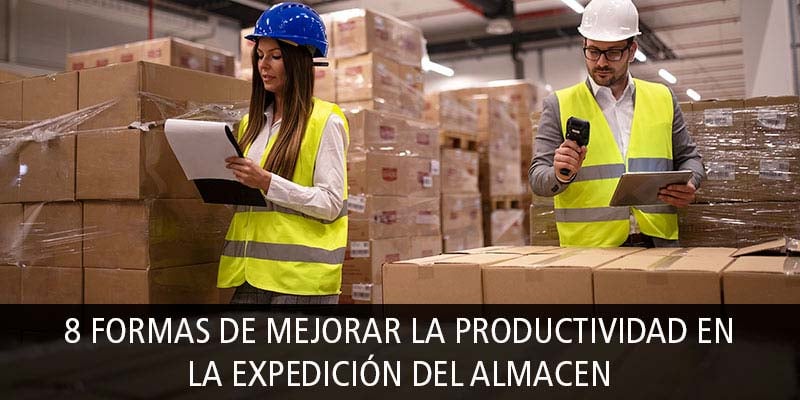
*
La expedición del almacén probablemente sea, si no la única, la parte de nuestro almacén que más y mejor percibe nuestro cliente. Es el final de la labor logística de todo almacén y donde se tienden a crear los mayores cuellos de botella que afectarán tanto a la cadena logística como de suministro. Los esfuerzos realizados en procesos anteriores pueden venirse abajo en este punto concreto por tanto es uno de los puntos fuertes para tener en cuenta a la hora de mejorar la productividad del almacén. Gran parte de esta productividad puede verse aquí comprometida.
Dentro de la expedición conviven procesos que van desde la preparación de los pedidos hasta la expedición propiamente dicha de los mismos. Esto significa que hablar de expedición comprende:
- los procesos de selección y recogida de existencias (picking).
- empaquetado y desempaquetado, combinación si procede, consolidación, acondicionamiento y carga de los pedidos.
- Además, tradicionalmente en esta fase final se ha utilizado la mano de obra de forma intensiva por lo que, surgen infinidad de oportunidades para reducir costos y tiempos, es decir, para mejorar la productividad del almacén,
Un exceso de inventario es un escondite ideal para los verdaderos problemas de productividad. Se hace tan habitual a nuestros ojos que acaba por desaparecer, como el paisaje que nos rodea.
De hecho, para evitar que nuestros problemas de productividad impacten en el cliente, casi sin darnos cuenta, aumentamos el nivel de inventario. Pero el problema de productividad, su causa raíz, no necesariamente tiene que estar en el almacenamiento, puede esconderse detrás de cualquiera de los procesos que conforman la expedición.
Por tanto, para poder abordar la mejora de la productividad en almacén tendremos que conocer exactamente cuál es la composición de cada uno de esos procesos que conforman nuestra expedición de mercancías. Es ingente la cantidad de factores que pueden afectar a la productividad del almacén en la expedición, pero podemos hacer un desglose de aquellos más importantes.
Factores que afectan a la productividad de nuestro almacén.
-
Movimientos
-
- Los movimientos de personas, que pueden ser en vacío o con carga, tanto si transportan mercancía solicitada como devolviendo producto sobrante.
- Los movimientos de mercancías, que deben desubicarse, ubicarse en otras zonas de picking o de expedición, desplazarse hacia la zona de embalarse, transporte de producto no usado y su ubicación, etc.
- Los movimientos de elementos auxiliares que deben utilizarse en el embalaje y acondicionamiento de la mercancía o del pedido para su posterior transporte y entrega y que también conllevan los mismos movimientos que el resto de las referencias, es decir, deben desubicarse, transportarse, usarse, retornarse y ubicarse de nuevo el sobrante. Muy importante ya que normalmente se dedica poco tiempo a su intralogística particular como si no se produjese un coste a la par que un consumo de recursos.
-
Elementos que influyen en nuestras técnicas operativas como:
-
- El layout, que afectará de forma directa e indirecta a muchos factores entre ellos los recorridos, la cantidad de desplazamientos y su longitud, los elementos de manutención que usaremos, los tipos de estanterías y su disposición y todo ello, claro, afectará al tiempo empleado en cada operación.
- La naturaleza de las referencias, resistencia, dimensiones, peso, fresco, congelado, seco, granel, etc. En la productividad también influye si manejamos una gran variabilidad de naturalezas que debemos combinar para conformar nuestros pedidos.
- Ubicación de las referencias, la disposición afecta a la productividad. así como la cantidad de referencias que manejemos y el control que tengamos sobre su localización, obsolescencia, disponibilidad, etc. Mayor número de referencias implica mayor complejidad en la expedición y por tanto exige una mayor optimización de procesos para su productividad.
- Líneas de pedido. ¿Manejamos gran cantidad de pedidos de pocas líneas, pocos pedidos de muchas líneas, ninguno de los anteriores o todos? ¿En cada línea se pide gran cantidad, poca cantidad, tenemos cantidad mínima? La cantidad de pedidos a preparar, la cantidad de unidades por línea, el tipo de embalaje e incluso el de cliente influyen en la operativa de nuestra expedición y por tanto contribuyen decisivamente a mejorar la operatividad del almacén o a su contraria.
-
Tiempos
-
- Tiempos administrativos, como el invertido en la preparación de la documentación, los listados de picking (si los debemos elaborar), preparación e impresión de etiquetado, envíos de correos, archivos, comunicaciones, etc.
- Tiempos de los desplazamientos, cuando hay personas son aquellos que realiza cada operario con carga o sin ella, pero si hay automatismos estos tiempos, aunque inferiores, también deben tenerse en cuenta ya que la mercancía se desplaza de un lugar a otro igualmente.
- Tiempos empleados en ubicar y desubicar todo lo necesario para la preparación, no sólo de las referencias. Muy variables dependiendo de nuestras instalaciones ya que en ello influye si tenemos zona de pre-picking, si usamos embalaje desechable o contenedores reutilizables, si debemos devolver producto sobrante o no, si usamos maquinaria adecuada o automatismos, etc.
- Tiempos no deseados, que en resumen son todos aquellos que se emplean en corregir errores o defectos e ineficiencias del sistema en general, por ejemplo, tiempo empleado en buscar una referencia que no aparece, en corregir algo que el sistema dice que está y no está, retirada de obstáculos, choques con instalaciones, etc. Se miden muy pocas veces, pero afectan de forma alarmante y siempre negativamente en la productividad.
De media, entre el 40% y el 60% de los costos operativos del almacén se concentran aquí
Esto puede darnos una idea de la importancia que tiene controlar cada proceso y cómo puede llegar a repercutir positivamente en la productividad.
¿Cómo podemos mejorar la productividad en la expedición del almacén?
1.- No se puede mejorar aquello que no se ha medido.
Y no podemos medir aquello que no hemos definido, así que lo primero que debemos hacer es definir cada una de las actividades de nuestros procedimientos y medir cada uno de ellos estableciendo los indicadores de desempeño adecuados en cada caso. Por mencionar algunos de los más importantes: líneas por pedido, líneas de picking por unidad de tiempo, líneas de picking por unidad de tiempo y operario, media de salidas por día, media de salidas por día en unidades de embalaje, rotación de inventario por ubicación de picking, líneas de reposición por unidad de tiempo y por ubicación, pedidos servidos frente a pedidos totales, líneas de picking completas frente a líneas de picking totales, y muy importante el porcentaje de nivel de servicio al cliente y el número y el tipo de incidencias en pedidos. Los indicadores son los prismáticos que nos permiten ver lo que está ocurriendo de verdad en cualquier proceso, sin ellos estamos casi ciegos.2.- No imponga más controles en proceso de los estrictamente necesarios.
Aunque utilicemos lectores eficientes de códigos de barras, si obligamos al operario a escanear el código de producto, el de embalaje, el de ubicación, el de contenedor, el del destino, a sí mismo, etc. antes de depositar la referencia para reponer una ubicación o antes de depositarla en el carro de picking, efectivamente ganamos control, pero a qué precio. La obsesión por el control puede llevarnos a situaciones verdaderamente absurdas. Si el seguimiento de una referencia es por número de serie sólo con escanearlo, el sistema ya sabe que no estamos fallando en absoluto y así lo indicará, no siempre es necesario obligar la lectura para el control de ubicación, quizá sólo con indicarlo en texto será suficiente y esto debemos tenerlo en cuenta para cada referencia.
Aunque hemos planteado una situación exagerada no descuidemos este punto, es de los más importantes.
3.- Respecto al picking.
En almacenes no automatizados, prácticamente el 50% del tiempo empleado en picking se emplea en los desplazamientos. Por tanto, cualquier cambio orientado a reducir los desplazamientos mejorará la productividad. En este sentido hay muchas acciones que podemos realizar entre las que destacamos las siguientes:- Agrupación de pedidos o líneas. Agrupar para mejorar la productividad es algo que funciona siempre. Agrupamos pedidos por rutas de reparto, por ruta interna, por zona, por cliente, por urgencia, por oleadas. Es de vital importancia que definamos los criterios que rigen en nuestro almacén al respecto y actuemos en consecuencia.
Por ejemplo, por definición muchos pedidos de pocas líneas conviene agruparlos por oleadas, pero no siempre. Puede que haya ciertos condicionantes como el tamaño de las referencias o su fragilidad, que hagan que nos convenga separar de este criterio ciertas líneas de pedido que deben cogerse de forma aislada o agruparse con otros pedidos similares.
En cualquier caso, cada empresa define sus criterios, pero agrupar implica realizar de la misma forma tareas idénticas y repetitivas lo que redunda positivamente en la productividad frente a los sistemas menos flexibles que no lo contemplan o directamente no lo permiten.
- Pick to light/ put o light – que directamente eliminan el tiempo perdido en la toma de decisiones no productivas y gracias a la gestión visual, agilizan ambos procesos de coger referencias en la cantidad y lugar exacto que corresponde y dejar referencias en aquellos pedidos que corresponde ya que ni siquiera hay que atender una pantalla. Los sistemas por voz o por realidad aumentada funcionan exactamente igual.
- Cambios en el layout – la disposición de nuestras referencias, de las estanterías, pasillos, pasos de peatones, etc. afecta no sólo a la hora de realizar el picking, también a la hora de reponer dichas ubicaciones de picking y de la multitud de tránsitos que deben ejecutarse coordinadamente para no entorpecerse unos a otros. Diseñar un layout es una tarea importante y que puede abordarse desde el principio con el objetivo de reducir desplazamientos. Por ejemplo, con la orientación de cada estantería de picking respecto a la zona de preparación de pedidos o acercando zonas que deban estar conectadas.
- ABC por rotación en el área de picking – sin necesidad de meternos en la disposición ABC/XYZ (que sería el siguiente paso), si calculamos el ABC de nuestras ubicaciones de picking descubriremos que menos del 20% de las ubicaciones se utilizan para conformar el 80% de nuestros pedidos. Si estas ubicaciones están juntas en la misma zona y la ruta está configurada de forma inteligente, los desplazamientos para esta operación se reducen rápida y drásticamente.
- Automatismos – sustituir el clásico operario a producto por un automático producto a operario, elimina gran cantidad de desplazamientos improductivos. Es la mercancía la que se desplaza y no la mano de obra. La cantidad de operaciones que el mismo operario que ya no debe desplazarse, puede ejecutar por unidad de tiempo, se multiplican considerablemente. Además, estos sistemas son tan eficientes que no admiten competencia, existen sistemas (que además son muy compactos) que con dos estaciones de picking (o entrada) pueden llegar a tramitar 400 líneas por hora de trabajo (de salida o entrada) pero pueden llegar a las 4000 líneas/ hora con cinco estaciones.
4.- Organización, orden y limpieza.
No hay nada más improductivo que ponerse a buscar aquello que nos hace falta para el desempeño diario, en la expedición suele ser “el precinto”, “la caja necesaria para embalar”, “la documentación”. En definitiva, la aplicación de herramientas Lean como las 5S orientadas a eliminar toda aquella tarea improductiva redundará en resultados rápidos y positivos.
5.- Estandarizar.
Estandarizar el caos no es productivo. Realizar una labor de estandarización en nuestros procesos que establezcan exactamente qué debemos hacer y como en cada caso, agiliza en general cualquier operación.
6.- Gestión documental y de la información.
La recepción y posterior gestión y expedición del pedido también es productividad y afecta a la operativa. Utilizar intercambio electrónico de datos, proveer de los medios y la capacitación adecuada, estandarizar o automatizar son opciones que también pueden aplicarse aquí.
7.- La maquinaria adecuada.
De qué sirve optimizar un proceso, organizar controles, establecer KPIs, capacitar al operario, optimizar la distribución y el embalaje si las horquillas de nuestra carretilla no llegan a la última altura de almacenamiento, o si no deja de estropearse la única carretilla que tenemos, o si la holgura que tiene impide trabajar con seguridad a cierta altura o si en algunos pasillos no puede girar. El mantenimiento de los elementos de manutención y su correcta elección adaptada a nuestras instalaciones es de vital importancia y uno de los puntos fuertes y de elevada prioridad si de verdad queremos mejorar en productividad.
8.- El software de gestión adecuado.
Lo hemos dejado para el final ya que entendemos que no sólo el software por sí mismo va a aumentar la productividad. El sistema SGA es una herramienta más de las muchas que debemos emplear de forma simultánea para mejorar, eso sí, es de las más importantes y efectivas. Un sistema ERP combinado con la potencia operativa de un sistema SGA es la combinación perfecta que nos permitirá entre otras cosas “ver” el almacén desde un cuadro de mando. La expedición y sus indicadores estarán controlados permanentemente por el sistema en tiempo real, algo imposible de lograr de otra forma. Esto nos permitirá tomar decisiones respecto al layout, respecto a la conveniencia de usar sistemas auxiliares y de apoyo al picking como un pick to light, respecto a qué partes y referencias automatizar, la mejor ubicación en cada momento para cada referencia, la mejor agrupación para nuestros pedidos y además controlando en todo momento el rendimiento de la mano de obra y los recursos empleados.
Conclusiones
Hablar de expedición es hablar de grandes movimientos de mercancías, de personas, de complejas operaciones de selección y combinación de referencias, de multitud de operaciones de ubicación y desubicación y de acondicionamiento. Debemos garantizar un flujo rápido y continuo en el comportamiento general de todo proceso y la expedición no es una excepción. Todos los esfuerzos de procesos previos resultarán infructuosos si en esta fase final el proceso pierde eficacia, eficiencia y se ralentiza.
La solución más recurrente siempre es emplear la mano de obra. Pero con ella traemos al proceso también todas sus ineficiencias. Con los medios a nuestro alcance hoy en día estamos viendo que la mano de obra suele ser el eslabón más débil en cualquier proceso y por ende el que marcará la resistencia total de la cadena.
La conformación de cada puesto de preparación de pedido, mantenerlos bien abastecidos de todo lo necesario para trabajar sin paradas, el trazado de rutas o el criterio de distribución de cada referencia en la zona de picking, la forma y el momento de la reposición pasando por la correcta elección y el mantenimiento de los elementos de manutención, todo influirá en nuestra productividad. Cada pequeño detalle es importante en esta fase porque ya no tenemos amortiguador que mitigue el golpe directo de una incidencia sobre el cliente.
La expedición es la fase final, la que nos define frente al cliente, la parte que se ve de nuestro almacén y la que culmina con éxito o fracaso todos los esfuerzos anteriores en la cadena. Además, es donde se concentran gran cantidad de recursos y tiempos muertos que, en realidad, no son sino multitud de oportunidades de mejora sobre las que podemos actuar y mejorar.
*Foto de Personas creado por aleksandarlittlewolf - www.freepik.es
También te pueden interesar...