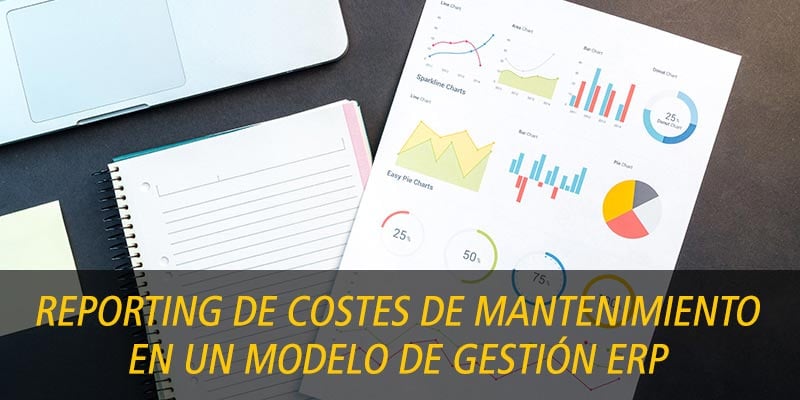
El reporting de costes de mantenimiento aporta una dimensión analítica de alto valor a los gerentes de esta área de responsabilidad, que pueden afrontar sus decisiones ejecutivas mejor informados a partir de los datos cosechados a lo largo del proceso de registro diario.
No obstante, no son pocos los retos asociados a esta fase final de análisis, y el uso de herramientas no integradas, como hojas de Excel (que requieren de la implementación de macros para determinar los indicadores de rendimiento), o cierto software de mantenimiento clásico (que requiere del lanzamiento de consultas SQL para cruzar tablas de datos), puede dificultar en gran medida la tarea.
Como veremos en la segunda parte de esta exposición, los nuevos recursos informáticos de gestión centralizada y las aplicaciones de mantenimiento dedicadas de nueva generación aportan funcionalidades propias del business intelligence para diseñar informes personalizados.
Control de costes de mantenimiento: mejores decisiones sobre los activos
Tener un modelo específico de asignación de costes de mantenimiento supone, para los responsables de este departamento, una capacidad mejorada para dedicar recursos y evaluar su desempeño. Así, una de las cuestiones de mayor relevancia en su proceder, y cuya resolución requiere de datos complejos sobre el equipo y las tareas de mantenimiento recibidas por el mismo, como es si continuar manteniendo el equipo en cuestión es más rentable o no que sustituirlo por uno nuevo, puede superarse de forma informada contando con registros centralizados del historial de reparaciones del equipo.
Asimismo, hacer un seguimiento de la dinámica de costes puede ofrecer una perspectiva mejorada de la evolución de las actividades organizativas. Especialmente, en iniciativas que aún no ha pulido un sistema procedimental de asignación de tareas y la estrategia principal de mantenimiento, analizar los datos de un período relativamente corto puede servir para inferir mejoras que pueden implementarse en base a las cifras cosechadas. Dichos KPI (indicadores), sin ayuda de una solución avanzada pueden ser difíciles de obtener, como anticipamos, a pesar de la relevancia de su monitorización constante.
Soluciones para la gestión del mantenimiento industrial
La nueva generación de componentes asociados al módulo central de un sistema de gestión ERP garantiza una integración total de los datos y un rápido acceso a la información derivada de la dinámica de trabajo establecida por este departamento. Al margen de las ventajas que nos ofrece a la hora de diseñar un plan de mantenimiento acorde con la estrategia de la organización, uno de los mayores beneficios se encuentra en el seno del reporting, concretamente en el envío de bonos por la intervenciones.
Una vez que un técnico ha recibido una asignación de trabajo como resultado de la planificación o de una solicitud puntual, podemos registrar en cada bono el tiempo invertido en un mantenimiento, los repuestos utilizados y las herramientas necesarias para su realización, entre otros muchos parámetros de seguimiento.
Si profundizamos en esta funcionalidad imprescindible para desarrollar un control de costes fidedigno y eficaz que sirva para mejorar la capacidad de decisión entorno a los activos, vemos que las tareas desglosadas están incluidas en el maestro homónimo, de manera que es posible registrar su impacto económico ágilmente. También se pueden agregar indicaciones de forma manual para aportar una capa de datos adicional que luego puede ser analizada a posteriori.
Otro de los ámbitos más interesantes en este sentido es el registro de los tiempos de parada de los equipos mantenidos, una información que desvela la verdadera operatividad de una máquina sometida a escrutinio. A partir de esta estimación, los responsables de producción, en colaboración con el departamento de mantenimiento, pueden determinar la línea a seguir en la próxima regeneración de activos o responder mejor a una nueva oferta por parte de un proveedor que aporta datos precisos sobre el impacto del mantenimiento de una nueva máquina.
En otro orden, podemos analizar el desempeño de cada técnico en términos de tiempo y eficacia, discerniendo, en cada caso, la tarifa imputable al bono en concepto de mano de obra. Sin la ayuda de este tipo de soluciones integradas, dicha tarea puede posponerse en exceso, motivando que las acciones correctivas dentro del departamento no lleguen a tiempo o, simplemente, no tengan lugar.
Con respecto a los consumibles y accesorios, tenemos la opción de incluir en el bono, de forma sistematizada, todos los repuestos que han sido necesarios para llevar a cabo el mantenimiento, ya se trate de productos del inventario o componentes externos que ha sido necesario adquirir puntualmente. Lo mismo sucede si la reparación ha supuesto la inclusión de mano de obra subcontratada, un criterio que puede relatarse igualmente mediante el envío de datos al módulo contable y al centro de costes correspondiente.
Analizando la información
Como decíamos, disponer de más información supone mayores garantías de éxito en la implementación y mejora de una estrategia de mantenimiento compleja, como pueden ser el mantenimiento preventivo o predictivo.
Gracias a las funcionalidades de reporting avanzado, es mucho más accesible plantear comparativas entre el rendimiento de una activo u otro. También, si se está en una fase de investigación con respecto a la eficacia del propio planteamiento estratégico, esta clase de ejercicios evaluativos pueden derivar en la implementación de una segunda fase optimizada basada en los datos recogidos en los bonos de mantenimiento.
Otros ratios que nos pueden informar sobre la validez de nuestras actuaciones y que pueden obtenerse como resultado de este proceso de recogida de información son el índice MTBF (tiempo medio entre fallos) o el MTTR (tiempo medio de restauración). Ambos criterios, por sí solos, dan cuenta de la fiabilidad de un activo y el impacto de su puesta a punto, respectivamente.
Una solución cómoda y eficiente
Cuando trabajamos con un CMMS (Sistema de Gestión de Mantenimiento Computarizado) integrado en tiempo real con el cloud ERP, el reporting de costes de mantenimiento se realiza como parte del proceso en sí mismo, de modo que no es necesario crear un modelo específico de registro de manera posterior. Por otro lado, la asignación contable representa fielmente el impacto económico en el libro de cuentas, ya sea a través de la actualización de existencias o el registro de operaciones asociadas a la subcontratación de las labores de supervisión y reparación de equipos.
También te pueden interesar...