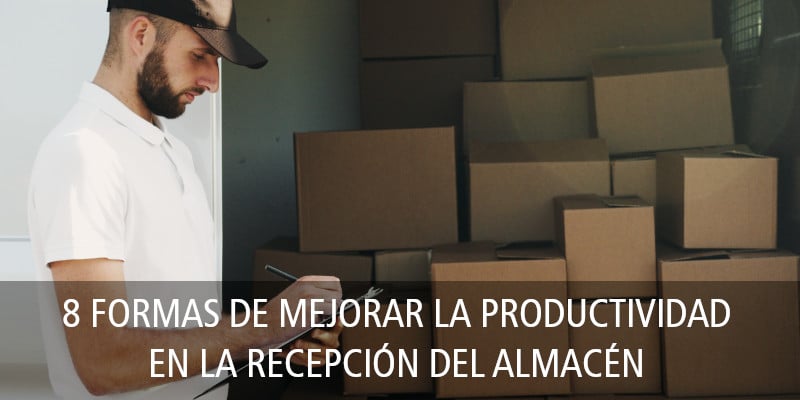
Parte del proceso de recepción es informar al sistema SGA (software de gestión avanzada de almacén), que su vez se sincronizará con el ERP cuándo y cómo entran las mercancías solicitadas. En qué muelle se realizará la descarga, qué referencias concretas han llegado, en qué cantidad exacta y en qué estado. Es la robustez de este proceso el que garantiza la precisión y seguridad de todos estos indicadores.
Este proceso requiere planificación e implica realizar movimientos de mercancías y personas, una cantidad nada despreciable de documentos e información, coordinar a la perfección muchos esfuerzos e innumerables tareas administrativas y operativas.
Cuando hablamos de mejorar la productividad siempre hablamos de eliminar todo aquello que suponga un exceso, un desperdicio o despilfarro, que en términos más concretos supone eliminar o reducir todo aquello que no agregue valor, pero que sí que suponga un coste.
¿Y qué tareas no agregan valor? Pues aquellas por las que el cliente no esté dispuesto a pagar. El almacén en su conjunto, como elemento regulador entre la oferta y demanda, es el que aporta utilidad a la propuesta de valor de la empresa, pero como en cualquier actividad económica, el almacén ejecuta su función sirviéndose de tareas que agregan valor y de otras que no lo hacen y es ahí donde debemos atacar si queremos mejorar la productividad. En concreto en un almacén los tiempos muertos, transportes y traslados y el mal uso del espacio, son los grandes focos de consumo de recursos y generadores de despilfarro.
Por tanto, y hablando concretamente de la recepción de mercancías, el primer paso debe ser siempre conocer a fondo nuestro proceso de recepción que comienza incluso antes de la llegada de mercancías a nuestras instalaciones.
Análisis de nuestro proceso de recepción de mercancías
El proceso puede dividirse en actividades previas a la llegada de la mercancía, actividades que se realizan cuando la mercancía ha llegado y finalmente actividades que se ejecutan tras la descarga.
Sin conocer el procedimiento no lo podemos mejorar.
Para poder mejorar la productividad debemos definir el proceso completo y resaltar aquellas tareas que consumen gran cantidad de tiempo y recursos. También las que resultan críticas en el proceso.
- ¿Qué debemos conocer de las tareas previas a la llegada de la mercancía?
Para ganar eficiencia en esta parte del proceso será necesario el trabajo intenso con proveedores y transportistas. Esta parte está repleta de burocracia y tareas administrativas conjuntas que pueden alcanzar niveles de eficiencia altos de una manera relativamente sencilla y a no demasiado coste.
Pero aparte de definir las tareas administrativas, podemos encargarnos de otros detalles con efectos incluso más directos en la operativa y cuyo descuido afecta negativamente a la productividad del proceso.
Elementos como:
-
-
- La cantidad y posición de la etiqueta en cada unidad de carga
- El tipo de código de barras o código QR utilizado
- La información que debe contener dicho código
- Si debemos recibir carga paletizada o a granel
- El número de paquetes por palé y de unidades por caja
- El peso y dimensiones máximas de cada unidad de carga paletizada
-
- ¿Qué debemos conocer de la descarga en sí?
-
-
- Calendario, fecha y hora de cada recepción.
- Si tenemos momentos de saturación y otros de inactividad y cuántos son.
- Si el transportista trae ordenada la carga o se dedica a reordenarla en nuestras instalaciones para su descarga.
- Si tenemos soluciones aparte para la mensajería
- Frecuencia de llegada de vehí
- Cuánto tiempo empleamos en el control de acceso (y pesaje si fuese necesario)
- Asignación muelle
- Tiempo y operarios empleados en la descarga
- Tiempo de conformación documentos
- Tiempo de salida de vehículo
-
- Y finalmente debemos definir las acciones necesarias tras la descarga
Que básicamente consisten en la parte de control y acondicionamiento de la mercancía para su ubicación: se cotejan albaranes, se reubican existencias, desmontaje y montaje de palés, cambios de palé si son necesarios y entrada de la documentación en el sistema SGA.
¿Cómo mejoramos la productividad en las entradas?
Vamos a centrarnos en los siguientes consejos:
- Evitar procesos redundados. Por ejemplo, es frecuente que un mismo albarán sea revisado más de una vez por varios departamentos. Por ejemplo, administración, compras y almacén. Debemos plantearnos si este exceso de controles es realmente necesario o simplemente responde a una cuestión nunca abordada del típico “siempre se ha hecho así”.
- Definir cada proceso: un sencillo diagrama de flujo, una secuencia de hitos del proceso o simples anotaciones de cada paso del proceso en orden y reflejando la documentación y la burocracia requerida en cada tarea, nos ayudará a detectar cuellos de botella, redundancias, sobreproducción, tiempos de esperas, etc. La idea es obtener una visión general de nuestro “modus operandi” de forma que cualquiera pueda ver y entender lo que sucede, cómo sucede y el tiempo que se emplea en cada fase de recepción.
- Establecer un sistema de indicadores: Una vez hemos definido cada proceso o cada parte del proceso es la hora de establecer los indicadores que van a servirnos de punto de control. Su misión es ayudarnos a visualizar la totalidad de nuestra situación actual. Es decir, nos ayudarán a detectar los puntos fuertes del proceso y también los cuellos de botella, pérdidas de tiempo o excesos, de manera que, una vez expuestos será más fácil mejorarlos.
No hacerlo así sería cómo circular sin indicadores de velocidad. ¿Cómo podríamos evitar una multa por exceso de velocidad si no tenemos cuentakilómetros? Probablemente acabaríamos yendo mucho más despacio de lo permitido para asegurarnos, lo que, en el mundo empresarial, también cuenta cómo despilfarro.
No podemos pretender implantar todo un complejo sistema de indicadores de golpe. El consejo siempre es hacerlo progresivamente empezando por aquellos que sean sencillos de calcular y que al mismo tiempo nos den una visión útil de la situación actual de algunos parámetros, por ejemplo: tiempo empleado por línea recibida (sabemos el total de líneas que recibimos en almacén y el tiempo total que cada operario emplea que normalmente es una jornada laboral menos los descansos), del anterior podemos deducir el coste por línea recibida, porcentaje de ocupación de cada muelle, tiempo medio empleado en cada recepción, tiempo empleado en cada recepción por proveedor, porcentaje de líneas recibidas sin incidencias respecto al total de líneas recibidas, volumen recibido por hora y operario, etc. - Trabajar con los proveedores aspectos que tengan que ver con cómo nos llega su mercancía. Aunque la rutina del trabajo nos impida verlo así en muchas ocasiones, cuando alguien quiere vendernos algo, lo lógico es que atienda a nuestras necesidades. Eso incluye las condiciones de recepción. Son detalles muy importantes la configuración del albarán, cómo debe venir empaquetada cada referencia, dónde deben ir colocadas las etiquetas, unidades por palé y por caja, alturas y dimensiones, pesos máximos, etc. No es lo mismo desde el punto de vista de nuestras entradas tener una forma diferente de recibir mercancía por cada uno de nuestros proveedores que tener una única forma de recibir, independientemente del número de proveedores que tengamos. Estandarizar el proceso elimina la variabilidad que es otra forma más de despilfarro.
- Etiquetado. Una forma de mejorar la productividad en nuestro almacén es marcar las normas de codificación de la información que nos llega en la propia mercancía, es decir, en su etiquetado. Decidir qué formato de etiqueta usar, qué tipos de códigos utilizar y qué información y en qué orden deben etiquetarse ahorra una cantidad de tiempo increíble sobre todo si trabajamos con lectores de códigos de barras.
El objetivo es eliminar todo el tiempo muerto que el operario debe emplear en la búsqueda y lectura de cada etiqueta y sobre todo que la lectura sea ágil y rápida y no esté plagada de errores que hagan que el operario se dedique mayoritariamente a borrar y releer (y enfadarse) cada bulto.
- Transportista – en ocasiones es el propio desorden en el transporte el que repercute negativamente en nuestra propia productividad. En numerosas ocasiones nuestros operarios esperan “parados” a que el transportista reordene su carga para poder obtener acceso a la nuestra. Incluso llegan a utilizar nuestros muelles para sacar mercancía ajena que le impide descargar la nuestra, con lo que además debemos esperar a que la vuelva a cargar disminuyendo la productividad del muelle en sí.
Siendo que es un proceso completamente externo, nunca debería repercutir sobre nuestra productividad ya que es una simple cuestión de orden. Por no invertir tiempo previo en organizar su carga en el orden inverso al que debe descargarse, traslada sus ineficiencias a nuestras instalaciones. Conviene medir en qué medida esta forma de trabajar externa impacta en nuestro rendimiento porque puede llegar a ser tan frecuente que nos sorprenda el resultado de averiguar hasta qué punto estas ineficiencias externas pueden generar horas extra, retrasos y pérdidas en nuestro almacén. - Muelles. Una forma de aumentar la productividad de cada muelle es establecer un calendario con fechas y horas de descarga. No sólo optimizamos el porcentaje de ocupación del muelle, sino que evitamos que los operarios de recepción estén constantemente interrumpiendo sus tareas para descargar un nuevo transporte imprevisto. Algo más que frecuente en nuestros almacenes.
Se trata de “aplanar” el ritmo de entradas evitando picos y valles de actividad. Curiosamente, esta programación favorece el hecho de poder dejar en la reserva recursos para imprevistos. - Sistema SGA (software de gestión avanzada de almacenes). Lo hemos dejado para el final para no centrar todas las soluciones en la tecnología. Sin embargo, es evidente que un software facilita mucho las cosas.
Por una parte, ayuda evitar la repetición de procesos o excesos de control. El intercambio electrónico de datos agiliza el intercambio de información y el software chequea cada albarán además de procesarlos como factura a posteriori y por otra, facilita los procesos operativos ya que sólo espera a que la información que recibe electrónicamente se compare con la realidad de la recepción en el muelle.
Nos ayuda a definir cada proceso ya que, para poder funcionar, un software debe tener meridianamente clara esta parte. Además, es el propio software el que establece un sistema de indicadores y nos los muestra de forma comprensible en un cuadro de mando para revisar rendimientos, detectar cuellos de botella e iniciar acciones de mejora.
Al tener medidos todos los procesos, la valoración y el trabajo con proveedores se facilita enormemente ya que podemos dirigirnos a una negociación cargados de datos y porcentajes de repercusión de sus ineficiencias en nuestra productividad del proceso. Esto también ayuda al proveedor o transportista a ver aquello que probablemente ni siquiera estén midiendo y, en consecuencia, a mejorar su propia eficiencia.
En resumen, un software ayuda a estandarizar cada fase del proceso de recepción y por tanto a mejorar la productividad global.
Un ejemplo
Veamos un ejemplo concreto. Una empresa de distribución tiene como producto estrella un cajón portamonedas (la versión actual de los de las cajas registradoras) que recibe en contenedores procedentes de Asia en varios formatos: manual, automático, blancos y negros. Para aprovechar el espacio del contenedor, compras, ha decidido que vengan sueltos y a granel, así pueden cargarse de cajones literalmente hasta el techo.
Una vez por semana llega el contenedor del puerto al almacén y cada vez se escuchan las protestas de los operarios al respecto porque todas las cajas por fuera son idénticas. Sólo se diferencian por una etiqueta (1 cm alta por 5 de larga) con un código de barras que viene en una esquina de cada caja. Dependiendo de la terminación y gracias a la experiencia de los operarios se sabe qué cajón es negro, blanco, automático o manual.
Cinco operarios se organizan para que el transporte esté el menor tiempo posible en el muelle ya que, además, hay penalización si se retiene al transporte demasiado tiempo. Buscan palés en el almacén (algunos ya están preparados, pero siempre falta alguno), dos descargan a mano, dos los depositan por color y tipo en palés monoreferencia y uno va retirando los palés que se van completando a una zona donde se revisarán y filmarán para ubicar.
Hemos obviado reflejar el tiempo que cuesta cada tarea porque realmente no importa, puede verse claramente cómo mejoraría la productividad, realizando acciones de proveedor que mejoraran la forma en que la mercancía llega a nuestras instalaciones.
A la izquierda la forma actual, a la derecha la futura donde el único cambio consiste en que la mercancía venga paletizada y correctamente etiquetada. En la parte derecha se han marcado en rojo las tareas que NO se realizan por venir la carga paletizada.
Además, la parte izquierda emplea a cinco operarios y la de la derecha sólo a dos en la descarga con carretilla eléctrica y uno en la lectura de etiquetas. Tareas que además pueden simultanearse con lo que cómputo total de tiempo de recepción, se reduce aún más.
Una de las tareas que más tiempo consumía era escanear caja por caja. Dado que en cada palé podían haber 40 cajas máximo, esto aproxima una idea del tiempo que se ahorraría tan sólo con esta acción.
En total un proceso que superaba la hora y cuarenta y cinco minutos sin problema empleando a cinco operarios, tan sólo con un cambio en el formato de la carga, no superaba la media hora empleando solo a tres y, además, en épocas de escasez de recursos (vacaciones, bajas), un único operario podía realizar el trabajo en menos de una hora. Por mucho que aprovechara el espacio del contenedor la carga a granel difícilmente justificaba el exceso de recursos empleados en la recepción además del riesgo de lesiones en ese tipo de descarga manual.
Conclusiones
Para mejorar la productividad en la recepción del almacén lo primero es conocer con gran detalle el proceso de recepción del almacén. Parece obvio y una redundancia en sí misma pero no son pocos almacenes los que pretenden mejorar a base de acciones esporádicas, sueltas, descoordinadas que producen poco o ningún efecto sobre su productividad.
Además, cada avance debe mantenerse en el tiempo. Por tanto, la mejora continua debe responder, en primer lugar, a una estrategia más amplia. Para establecer una estrategia primero debemos conocer cada paso del proceso a mejorar, luego debemos medir cada uno de esos pasos o partes importantes de ellos.
Medir significa transformar en números lo que vemos físicamente. Luego debemos reflejarlo todo en un cuadro de mando, un tablero, un papel, un soporte que nos dé una visión global de lo que está ocurriendo y así poder iniciar acciones de mejora donde sean más efectivas o donde sea sencillo aplicarlas con resultados notables. De nuevo mediremos el efecto de estas acciones y el proceso vuelve a comenzar.
¿En qué queremos medir nuestra productividad? ¿Líneas recibidas por hora, horas operario por descarga, segundos por línea, volumen recibido por muelle? Debemos decidir dónde marcaremos los puntos de control y decidir dónde se encuentra el punto de partida.
Mejorar la productividad es un camino circular que nunca acaba, si no definimos dónde está el comienzo y los límites del trayecto, no podremos saber cuántas vueltas hemos dado ya o si nos hemos desviado definitivamente del mismo.
*Foto de Artem Podrez en Pexels
También te pueden interesar...