Qué es Picking
En este artículo nos vamos a centrar en una de sus modalidades, el picking en recorrido también llamado picking operario a producto, pedido a pedido. Veremos algunas formas de organizarlo, válidas tanto si el picking se realiza en un almacén con fines de distribución comercial, como para abastecer una cadena de producción.
El picking es el proceso de almacén, enmarcado en la cadena logística, mediante el cual procedemos a la rotura de la unidad de carga inicial, es decir, la de transporte o almacenamiento, para generar otra que será o formará parte de la de expedición: del pedido a cliente. Este proceso puede suponer entre un 12% y un 60% de los costes relacionados con las operaciones de almacén. Es una de las tareas que más recursos laborales, de infraestructura y administrativos consume, imprescindible para dar servicio al cliente y que por desgracia no aporta valor pero sí coste. Ejecutar el picking eficazmente al menor coste posible y mejor que la competencia, puede suponer una ventaja competitiva.
Dentro de lo que supone la preparación de pedidos hay que tener en cuenta que sólo los desplazamientos suponen entre el 50% y el 70% del tiempo empleado. Por eso el sistema de ubicación que utilicemos redundará directamente en la ejecución de nuestro picking. Lógicamente ubicación y picking son conceptos estratégicos indisociables.
ABC por Rotación
El SGA será el que nos haga el cálculo del ABC por rotación, la estrategia de ubicación que llevaremos en nuestro almacén determinará la longitud y duración de los desplazamientos y por tanto la organización del picking en recorrido. El único “pero” que tiene la clasificación ABC por rotación como criterio de ubicación para el picking, es que el mercado hará variar el ABC y por tanto el mix de artículos. Esto provocará cambios en la estrategia, por lo que debemos fijarnos períodos de revisión del ABC para asegurarnos su efectividad.
Densidad de preparación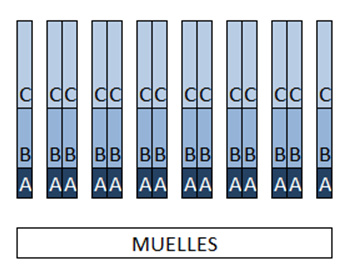
Otra magnitud en la que debemos fijarnos es la densidad de preparación, es decir, la relación existente entre las líneas que nos están pidiendo respecto al total de ubicaciones disponibles para el picking. En almacenes donde la densidad de los pedidos sea alta, el picking en recorrido probablemente nos dará una productividad adecuada.
En la figura podemos ver una distribución clásica para almacenes que suministran a empresas de gran volumen y muchas líneas por pedido. Ideal para picking en recorrido. En esta distribución varios pickers operan simultáneamente en varios pasillos haciendo cada uno un pedido distinto por recorrido. No importa si el picking es en altura o a nivel de suelo, sólo hay que tener en cuenta el espacio disponible para cada picker o el orden de salida, adecuándolo a sus medios de manutención para evitar que se molesten entre sí.
Una versión reducida de esto mismo es el picking realizado para una cadena de montaje en secuenciación. Desde el punto de vista de una sola célula de picking, consideraremos cada orden de secuencia como lo que es, un pedido muy reducido de pocas líneas, por tanto la distribución anterior (en versión reducida) sería igualmente válida aunque cada picker trabajaría en una célula separada de las demás para facilitar su reposición por el lado contario al que está trabajando el picker. En estos casos en que el trayecto del picker es de corto recorrido, los tiempos de ejecución son extremadamente justos, el nivel de servicio exigido por el cliente es del 100% y los costos de incumplimiento elevados, es aconsejable que el SGA, aparte de guiar al picker se apoye y controle en otros sistemas como el pick to light.
En ese caso el SGA va emitiendo etiquetas de código de barras en cada célula, una etiqueta por secuencia. El picker captura con un lector el número de secuencia y el SGA al recibir esta información ilumina los puntos de pick to light donde el operario debe coger cada pieza de dicha secuencia. No los ilumina todos a la vez sino en el orden adecuado para hacer el recorrido lo más corto posible.
Para evitar equívocos el SGA no ilumina el punto siguiente hasta que no recibe la información del picker de que ha ejecutado la acción anterior.
¿Cómo informa el picker al SGA de que ha terminado el picking de cada fracción?
Una posibilidad muy segura, es que una célula fotoeléctrica, similar a la que tenemos en las puertas de los ascensores, colocada estratégicamente en la ubicación de cada referencia, detecte el movimiento del picker al coger la referencia. El SGA da la referencia por secuenciada e ilumina la siguiente posición, así hasta terminar con todas la que dicha secuencia requiera. Otra posibilidad es colocar un botón que debe pulsarse al acabar cada picking.
Esta sería una modalidad de picking mixto. Por un lado es el operario el que se desplaza hasta el producto, y por el otro es el producto el que es acercado al operario. De esta manera el recorrido de picking se reparte entre el picker y el elemento electro-mecánico que repone las referencias que se van agotando. Eso lo hemos visto muchas veces en su versión más simple de estanterías de roldanas o dinámicas por gravedad.
Picking en Recorrido
Una organización más clásica del almacén para picking en recorrido es la que vemos en la siguiente figura de la derecha. En esta ocasión, si disponemos de pedidos muy largos de piezas pequeñas, podemos habilitar las ubicaciones a nivel de suelo para picking y las de la parte superior de reserva para reposición. En esta ocasión debemos tener en cuenta que la mayor parte de los recorridos se concentrarán en el pasillo flanqueado por las estanterías de referencias “A”. Pero a cambio es una distribución que facilita mucho el seguimiento y control y puede combinarse con políticas de ubicaciones fijas.
Flexibilidad en la solución
En realidad no hay una solución única para cada cuestión logística, normalmente las soluciones parten de un único problema pero se resuelven con combinaciones de distintos sistemas. Quizá nuestras referencias “súper A” no requieran picking y se trasladen en palé completo directamente desde sus ubicaciones a la zona de consolidación que puede ser el mismo muelle de expediciones, al mismo tiempo el picking para las referencias A y B se pueden estar realizando en recorrido, pedido a pedido, a nivel del suelo en la zona de los A y picking en altura en la zona de los B y las C y D, se realicen por oleadas.
Por eso mismo el SGA está preparado para trabajar de formas diferentes en cada uno delos diferentes sectores de nuestro almacén, debe tratar de forma distinta a distintos grupos de referencias, debe atender al mismo tiempo a diferentes necesidades del mercado, de nuestra cadena de producción, de nuestros clientes y de nuestros proveedores, trabaja en series de pedidos cortos y en cadenas más largas, en recorrido y por oleadas, debe gestionar y coordinar automatismos, pick to light y estar preparado para recibir otros avances que vendrán.
Puedes ver mas informacion del modo de trabajo de un almacen con SGA en nuestros post anteriores:
- Comparativa: Como se recibe mercancia con SGA y sin SGA.
- Como se trabaja en un almacén con SGA y sin SGA.