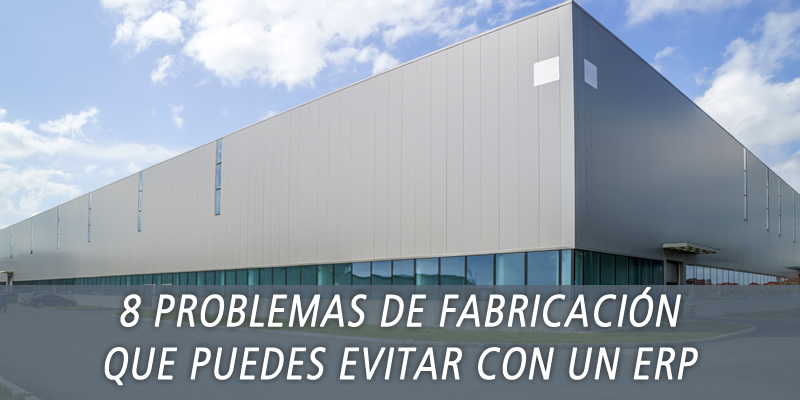
En la actualidad, la eficiencia de una empresa debe formar parte de su ADN, cuanto mayor sea, mejores resultados obtendrá en un mercado que es cada vez más competitivo. Las inversiones que realice la empresa debe hacerlas buscando conseguir esa máxima eficiencia en todo momento. Acabar con los problemas relacionados con fabricación de una manera rápida y sencilla forma parte de este proceso.
Una de las soluciones es la utilización de un software ERP. Concretamente, podríamos enfocarnos hacia un ERP de fabricación, una adaptación del sistema pensado para este tipo de empresas. Pero, sin duda, la mejor manera de conocer sus ventajas es saber qué tipo de problemas puede resolver.
Las soluciones que aporta un ERP industrial
Un programa de estas características está pensado para mejorar la eficiencia de una empresa de fabricación de una manera sencilla. La acumulación de datos en una sola fuente ayuda a generar una mejor comunicación entre los diferentes departamentos, evitando duplicidades y otros tipos de problemas.
- Control de inventario
Contar con un inventario adecuado en todo momento es fundamental para poder hacer frente a los pedidos de los clientes. Al mismo tiempo, un exceso de materiales o de productos suele conllevar otros problemas de gestión que afecta a la eficiencia del sistema productivo. Contar con un ERP permite controlar todo el proceso desde la compra hasta la venta, pasando por la fabricación. Se trata de una manera más eficiente de controlar todo el proceso. Si se venden bicicletas, el programa detecta para cada pedido de venta, si hay stock de producto terminado o, en su caso, tiene los componentes para fabricarla. - Control de materias primas
Ligado al punto anterior, en muchas ocasiones las materias primas de la que se dispone la empresa pueden estar en nuestro almacén o en el de terceros (depósitos en los almacenes de los proveedores). El ERP contempla los datos de los que dispone para generar una planificación de la materia prima necesaria para afrontar la producción en activo y la esperada, pudiendo generar de manera automática las órdenes de compra y todos los ajustes que sean necesarios. Continuando con el ejemplo anterior, sabremos con antelación las ruedas y cuadros que necesitamos para hacer frente a los pedidos que vendrán o ya están en marcha. Al mismo tiempo, podremos ser rigurosos con los tiempos de entrega al conocer si necesitamos algún material. - Trazabilidad del producto
En cualquier empresa de fabricación es importante conocer todos los pasos que sigue el producto, desde que comienza su fabricación hasta la entrega final al cliente. Un problema bastante común que se puede dar en estas empresas es un error en la cadena de producción. Contar con un sistema integrado permite detectar estos errores y evitar que se vuelvan a producir. Pero cobra especial importancia en las empresas de ciertos sectores, como por ejemplo las de alimentación donde dicha trazabilidad es obligatoria. Contar con un único sistema que lo gestione permite obtener un gran resultado así como seguridad. - Reporte de datos
Los cientos de papeles no ayudan a realizar una correcta gestión, esto puede provocar la pérdida de información relevante o simplemente la desaparición de un envío. Contar con un ERP soluciona este problema al volcar todos los datos sobre él. Esto permite mantener actualizado el sistema y que emita información en tiempo real para ayudar a la toma de decisiones. - Evitar retrasos
Es muy común acumular tiempo de retraso en un envío por problemas en todas las fases anteriores incluida la producción. Esto puede resultar incómodo tanto para el cliente como para la empresa. En muchas ocasiones este problema viene derivado de errores subsanables gracias al uso de un sistema ERP. Apoyándonos en él evitamos errores como la falta de materias primas, informar de plazos imposibles o fallos en el inventario del almacén. - Duplicidades de fuentes de datos
Contar con varias fuentes de información independientes es un error. Un ejemplo de ello es que el Departamento de Ventas, el de Facturación y el de Producción cuenten con sistemas separados. Esto puede provocar que de un pedido pueda tener información inconsistente en las tres secciones comentadas. La solución es sencilla: usar una sola base de datos. Ventas volcaría en ella el pedido y el resto de los departamentos trabajarían sobre la información ya establecida. Este proceso lo permite un sistema ERP que, además, ayuda a aumentar la información disponible en un pedido. - Requisitos legales
Si la empresa se dedica a realizar un proceso productivo que en muchas ocasiones exporta, es importante contar con la documentación asociada al lote para pasar fronteras y aduanas. Esto permite mantener de una manera sencilla toda la información sobre un pedido en un solo lugar, unificando todos los datos necesarios para los trámites legales relacionados con él. - Rentabilidad
Pero, sin duda, el gran problema que resuelve un ERP es la pérdida de rentabilidad. Tener procesos duplicados, la necesidad de realizar comprobaciones con otros departamentos o el simple hecho de tener errores en el inventario provoca una pérdida de tiempo en la cadena de fabricación. En la actualidad esos errores hacen reducir la competitividad de la empresa de forma significativa. Contar con un software perfectamente integrado ayuda a hacer frente a todo este tipo de problemas que pueden surgir en el día a día de una empresa.
Conclusiones
En todas las empresas existen 2 procesos críticos con relación a la satisfacción de sus clientes:
- El momento de entrega de su propuesta de valor (productos y servicios en un contexto y con unas condiciones).
- El control del almacén como elemento regulador entre los pedidos de clientes y la disponibilidad de productos en las condiciones establecidas.
Ambos procesos requieren una gran coordinación entre todas sus actividades implicadas, pero en particular el último necesita, además de una perfecta coordinación, una gran eficiencia en su desempeño para que su gestión no influya negativamente en los costes. Es precisamente en esta área, donde el control de la fabricación (en empresas industriales) supone un elemento crítico porque suele ser uno de los procesos que más valor añade a la propuesta de valor de la empresa. Además, pensemos que todos los errores cometidos a lo largo de su cadena de valor son acumulables, por lo que hay que centrar el esfuerzo en evitar que dichos problemas sucedan en las fases más tempranas del sistema, ya que, de lo contrario, será muy difícil aplicar soluciones eficaces.
La importancia de centrar nuestro interés en la fabricación es precisamente porque está en el centro de todos estos procesos y, por tanto, está muy condicionada por todo lo que pase a su alrededor. Sólo un sistema de información integrado, como es el caso de un ERP, puede ayudar a gestionar de forma eficiente las distintas actividades, ya que requiere una comunicación ágil, única, y precisa sobre la que se apoyen las decisiones de los responsables de gestionarlas.
Confiar en profesionales nos ayudará a evitar estos conflictos que pueden surgir en la adaptación del nuevo sistema. Nos darán los consejos necesarios para realizar una transición lo más sencilla posible. Dos de los más importantes que debemos evitar es la falta de planificación y el no incluir al usuario final en el desarrollo.
La mayoría de los problemas de fabricación tienen una sencilla solución con el uso de un sistema ERP, pero es importante saber cómo realizar una buena implementación para así reducir los problemas y no hacerlos crecer.
Si te ha interesado este POST te invitamos a que leas también:
- ¿ QUÉ ES UN ERP ? EL SISTEMA DE GESTIÓN INTEGRAL POR EXCELENCIA
- 5 FALLOS COMUNES EN LA GESTIÓN DE ALMACENES Y SUS SOLUCIONES
y si quieres conocer una herramienta de ERP: