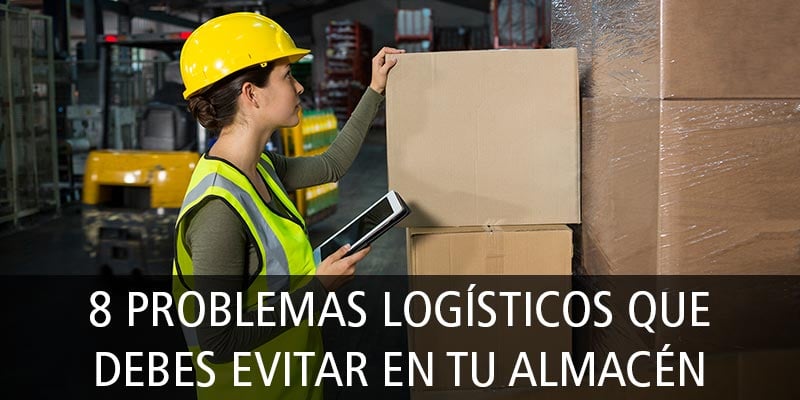
*
No es necesario resignarse a seguir sufriendo los problemas logísticos de nuestro almacén. Si bien es cierto que ninguna solución es sencilla, ni rápida por desgracia, es igualmente cierto que hay pocas cosas qué con trabajo, esfuerzo y perseverancia, por supuesto utilizando las herramientas adecuadas y poniéndolas en manos formadas, no acaben solucionando.
“Para evitar los problemas del almacén es necesario prevenirlos, no parchearlos”
Prevenir implica planificación y anticipación y su reverso, parchear, implica que no hemos prevenido y que el problema ya está haciendo de las suyas para instalarse definitivamente en nuestra organización.
Hablamos de un cambio cultural y de enfoque de visión:
- El almacén gestiona grupos homogéneos de referencias que, entre sí, resultan ser bastante heterogéneos, sin embargo, tratamos de almacenarlo todo en el mismo tipo de estantería de siempre, la convencional.
- La falta de organización, que se manifiesta en las individualidades campan a sus anchas por la solera de nuestras instalaciones y el talento se pierde sólo por el hecho de que no se gestiona, ni bien, ni mal.
- No se recopila información y esto provoca que su uso no acabe dando frutos lo que a su vez provoca “falta de fe” en la información, un círculo vicioso muy poco productivo.
- Seguimos creyendo que lo que siempre ha funcionado siempre funcionará sin darnos cuenta de que, si es afirmación fuese cierta, seguiríamos almacenando grano en silos de adobe y transportándolo en alforjas.
“Conocer a tu enemigo mejor que a tus mejores amigos”
Quien tiene la información tiene el poder de manejarla en su provecho. Si además podemos recopilarla en tiempo real, tenemos el poder de aprovecharla justo en el momento necesario, y aplicarla en el lugar adecuado, es como la logística de la información. Ese manejo preciso y quirúrgico de la información es la base de una buena gestión que evite cualquier problema previsible y afronte con mejores armas los imprevisibles.
Problemas comunes en los almacenes
Identificar los problemas es el primer paso para resolverlos y en el futuro para evitarlos. Por esa razón, vamos a tratar de hacer visibles algunos de los principales escollos entre los que nuestros almacenes se tienen que manejar hoy y que, en la medida de lo posible, deberíamos evitar.
1.- Convencional para todo.
Un lugar para cada SKU (Referencia de Almacén) y cada SKU en su lugar. Esta frase sigue siendo, o bien la menos presente o la más reinterpretada todavía hoy en multitud de nuestros almacenes. En plena era de la logística 4.0 y enfilando ya la recta final del primer cuarto del siglo XXI, seguimos aferrándonos a las viejas costumbres.
Pues no, no todos los artículos que debemos gestionar deben almacenarse en estanterías convencionales, aunque por su peso y dimensiones “quepan”.
Si no tenemos la suerte de almacenar unidades de carga homogéneas en tamaño, peso y forma, deberíamos realizar el estudio pertinente que, atendiendo a las características logísticas de las referencias que debamos gestionar y/o a su naturaleza, nos permita asignar los recursos, elementos de manutención, instalaciones y EPIs adecuados a cada una de las exigencias de almacenamiento que cada grupo de artículos requerirá.
2.- Desorganización de las referencias.
La distribución de las referencias dentro del almacén debe seguir un criterio adecuado y lógico, que persiga un objetivo concreto. Aunque carezcamos de programa SGA podemos realizar el cálculo del ABC sobre nuestras referencias y reconfigurar su distribución en nuestras estanterías, si no de la totalidad, al menos sí parcialmente, por ejemplo, sólo de las A.
El objetivo es mejorar su control, reducir la manipulación y sobre todo tiempos y recorridos. Si además logramos ubicar en la parte superior, las referencias estocadas que deben reabastecer las ubicaciones de picking, estaremos mejorando notablemente varias operaciones dentro de nuestro almacén con poco esfuerzo e inversión.
3.- Seguir viendo el almacén como un ente “aislado”.
Uno de los problemas logísticos más frecuentes, es el hecho de que muchos directivos de nuestras entidades son conocedores de las múltiples ventajas de la integración de la cadena de suministro, pero en la práctica, muy pocos enfocan realmente su actividad en llevarla a cabo.
Quizá una de las razones sea el celo que mantenemos con el flujo de la información que consideramos “delicada” para nuestra organización, cuando la integración real de la cadena de suministro se basa precisamente en compartir información. Un ejemplo muy concreto de esta realidad nada productiva sería la casi inexistencia de aplicación en nuestros almacenes de proyectos de administración de inventarios por los proveedores como VMI (Vendor Inventory Management).
VMI tiene su razón de ser en la creencia de que el proveedor está en mejor posición que nosotros a la hora de manejar su inventario, aunque se almacene en nuestras instalaciones. El proveedor conoce mejor sus tiempos de abastecimiento o manufactura y sus plazos de entrega y con una visibilidad total y en tiempo real de nuestras necesidades de inventario, es capaz de abastecernos con mayor eficacia y a menor coste que nosotros mismos. Eso significa, y ahí radica el problema, que el proveedor debe tener acceso a cierto nivel de tecnología, voluntad real de colaboración, grandes niveles de compromiso y visibilidad completa acerca de nuestro volumen de ventas, costes, cambios en los niveles de stock, programación de la producción, incidencias, etc.
Para implantar este tipo de proyectos, es posible que uno de los mayores problemas logísticos de nuestros almacenes sea, que también almacenen desconfianza.
4.- No implantar una cultura de mejora continua.
El verdadero problema es la inexistencia de este tipo de cultura y no solo en el almacén, sino en toda la organización.
Muchos lo publican, menos lo intentan y muy pocos lo consiguen. ¿Por qué? Porque lograr la verdadera implantación de la mejora continua implica realizar un cambio cultural radical y total en la organización. Es decir, para llevarla a cabo, hay que creérsela de verdad y además transmitirla, y no tomarla solo como acción de márketing.
Una verdadera lástima, porque la inmensa mayoría de los problemas logísticos y la práctica totalidad de los problemas del almacén, se resolverían sólo cambiando algunos hábitos, que a la larga produjeran el cambio cultural necesario y colaborativo hacia la mejora continua.
Una organización con veinte empleados y con una persona responsable de implantar mejoras, suponiendo que consiga llevar un ritmo de una acción de mejora al mes, implanta doce al año, y eso suponiendo que todas tengan éxito.
Una organización de veinte empleados implantando una mejora al mes por empleado implanta doscientas cuarenta mejoras al año, y gracias a que las ideas surgen de los propios empleados y que su actitud cultural se enfoca en mejorar y no en protestar y quejarse, prácticamente la totalidad de esas mejoras acabarán implantándose realmente. En eso radica el éxito del cambio cultural.
5.- Trabajar en diferido.
Es uno de los problemas más extendido del almacén, en algunas ocasiones e incomprensiblemente, incluso teniendo acceso a un programa SGA.
Sin entrar en las razones, que son múltiples, aunque la excusa más frecuente es la falta de tiempo o la urgencia, en multitud de almacenes se realizan acciones como empezar a mover o tomar referencias físicamente sin reflejar esos movimientos en el programa SGA. Esto sólo hay una forma de hacerlo: obligando al sistema a gestionar unidades en negativo para que luego “supuestamente” se compense, lo que nunca ocurre.
Esta insana costumbre provoca errores graves en el flujo de información, elimina la fiabilidad de los niveles de inventario y a partir de ahí, todo lo que funcione gracias a mantener la precisión de esos niveles se descompensa, creando cada vez más y más problemas, urgencias y negativos.
Es el círculo vicioso del almacén que se despega de su flujo de información.
6.- Tener información relevante (KPIs) y no hacer uso de ella.
Al menos no hacer el uso adecuado.
Cuando hablamos de gestión de stocks sobre todo estamos hablando de recopilación y manejo de los indicadores del desempeño o KPIs. Éstos deben cumplir una serie de normas, deben ser medibles, comprensibles por aquellos que los deben manejar y controlables, es decir, debemos poder manejarlos y actualizarlos constantemente para que resulten útiles.
Además, parte de los problemas logísticos se anclan en nuestros almacenes porque simplemente ignoramos la presencia de nuestros indicadores. Tenemos los datos, los podemos ver, manejar y medir, pero no los transformamos en información útil para la toma de decisiones.
7.- La organización de los equipos de trabajo.
Muy relacionada con su capacitación. Si queremos dar un servicio diez, no esperemos conseguirlo con un personal capacitado al cuatro y medio. Es nuestra responsabilidad como gestores de nuestro stock, capacitar y organizar al personal que de facto “realiza el servicio”, además de dotarlos con los medios y capacidades adecuadas.
Formación e información continua de los nuevos recursos disponibles para la realización de su trabajo, formación en seguridad laboral, en buenas praxis de trabajo, en nuevas herramientas y técnicas de trabajo en equipo, el liderazgo, colaboración, gestión de proyectos. Los campos de capacitación son infinitos y nunca debemos olvidar que dentro de esa formación deben estar incluidos aquella parte del personal que debe dirigirlos.
La aplicación de Lean Warehousing, es decir, la aplicación de las técnicas organizativas de Lean Manufacturing, la reorganización de nuestros almacenes en GAPs, que tantos éxitos organizativos y buenos resultados están consiguiendo en la industria, resulta ser un paso fundamental que ningún software ni ningún avance tecnológico hoy en día nos va a proporcionar.
Definir, configurar y capacitar a nuestros equipos de trabajo, es todavía un territorio reservado al ingenio y perseverancia humanos.
8.- Desactualización: seguir trabajando sin un programa SGA.
Nuestro almacén debe seguir el ritmo de los tiempos o resignarse a desaparecer.
Si vivimos la era de la digitalización, si de hecho estamos aún en los comienzos de la era 4.0, no debemos esperar que nuestro almacén siga manejándose con herramientas y técnicas del siglo pasado.
El primer paso hacia el camino de la digitalización es el programa SGA. Nos permitirá tener acceso en tiempo real a los principales KPI, extraer de ellos toda la información necesaria, podremos utilizar esa información para la toma de decisiones, nos permite “ver” qué ocurre en nuestro almacén, optimizar recorridos, mantener una perfecta trazabilidad, configurar las mejores ubicaciones, llevar diferentes tipos de gestión por zonas, rotaciones, etc. Asignar operarios a determinadas acciones, reorganizar el almacén según el ABC, trabajar en picking por oleadas, agrupaciones, urgencias, preferencias, en definitiva, nos permite entrar en el siglo XXI y gestionar adecuadamente nuestro stock y alcanzar el máximo nivel de servicio. Además, nos facilita el acceso a la base de la construcción de una cultura de mejora continua que es la información.
Digitalizarse o morir, esa es la verdadera cuestión.
Conclusiones
La inmensa mayoría de los problemas logísticos presentes en nuestro almacén vienen originados por la cultura de la empresa que los sufre.
Una cultura del esfuerzo, reorganización, apertura al cambio, mejora continua, resolución de problemas en equipo basada en la colaboración, el manejo de datos e información y el avance tecnológico, soporta muchos menos problemas que una cultura de gestión tradicional basada en el individualismo, la inmovilidad, la rigidez en la escala de mando, la organización de referencias sin método, la escasez de datos y la escasa fiabilidad de los existentes.
No existe un área específica del almacén que sufra más que otra, cuando el mal se instala en un almacén, suele extenderse y ser generalizado. Podemos estar convencidos de que la estantería convencional puede con todo, pero el hecho es que el resto de las instalaciones del mercado, no han surgido de la nada, sino que responden a la multitud de necesidades que conviven en un mismo almacén.
Quizá algún día se imponga el pensamiento más lógico que indica que lo que siempre ha funcionado, no garantiza que siempre vaya a funcionar, y las empresas asuman que viven en un ambiente de cambio constante al que deben adaptarse igualmente, de forma constante. Que la rigidez en la toma de decisiones solo genera más, y más problemas sin resolverlos nunca del todo. Que la información es la base de todo nuestro mundo, es lo que más valor aporta a las organizaciones. Pero no cualquier información, sino la información basada en la recopilación de datos en tiempo real, sometida a técnicas modernas de computación, es decir, la que ayuda en la toma de decisiones. Quizá logremos capacitar a nuestro personal de almacén para que nos ayuden a afrontar esta nueva era de digitalización con éxito.
Pero hasta entonces, nos queda un largo y muy interesante camino, lleno de logros y fracasos. Fracasos que nos harán aprender para enfocar mejor los siguientes retos. Esa es la visión de los proyectos que conseguirán evitar los problemas logísticos de nuestro almacén, en el presente y en cualquier escenario futuro.
*Foto de Tecnología creado por wavebreakmedia_micro - www.freepik.es
También te pueden interesar...