*
Un transelevador es un elemento de manutención robotizado y automático para tareas de almacenamiento en un almacén. Es el sistema más común dentro de lo que se conoce como sistemas AS/RS que son sistemas automatizados de almacenamiento y recuperación que, utilizando una combinación de equipos y software, gestionan tanto el almacenamiento como la ubicación y recuperación de mercancías.
Tabla de contenidos:
¿Cómo funcionan?
Estos elementos (transelevador) están compuestos de cuatro partes principales:
- la columna,
- el tren de rodadura,
- el armario con los componentes electrónicos
- y la mesa (cuna) con las horquillas o el sistema de extracción que se le haya incorporado (admite varios).
El sistema necesita de una cabecera o punto de entrada/salida que no es sino una ubicación donde se depositan las cargas recuperadas y donde las entrantes esperan su turno de almacenamiento. Aquí se realiza un control de galibo y de peso, para asegurar que las dimensiones y pesos de la unidad de carga entran dentro de las tolerancias del robot.
Cada transelevador se desplaza de manera autónoma a lo largo y ancho de un pasillo estrecho (unos 1.5 m) realizando movimientos de traslación y elevación (ejes x, y) de su cuna de manera que se encarga del transporte, almacenamiento y extracción eficientes de la mercancía desde y hasta las ubicaciones de las estanterías instaladas a ambos lados del pasillo.
Estos elementos ofrecen la posibilidad de ejecutar sus movimientos de ubicación y extracción de forma independiente en lo que se conoce como ciclo simple, o de forma conjunta en lo que se denomina ciclo combinado. La diferencia es que mientras que un ciclo simple sería el movimiento estándar de un transelevador al almacenar una mercancía, el combinado consiste en que el transelevador deposite una mercancía y recoja otra en un solo movimiento, mejorando el rendimiento y la agilidad de las operaciones logísticas.
Consideraciones previas de los transelevadores
Dado que los transelevadores son robots qué básicamente se dedican a coger unidades de carga de su cabecera y ubicarlos en celdas, de dimensiones predeterminadas e invariables, o extraerlos realizando la operación inversa, antes de trabajar con ellos, debemos tener en consideración algunos detalles.
- Es imprescindible disponer de un software SGA para poder trabajar con un transelevador: aunque su propio software será el que controle sus servomotores para que ejecute las órdenes de almacenamiento y recuperación, el sistema SGA será quien controle todos los procesos del almacén, incluido el flujo de materiales y la disponibilidad de recursos como el robot, es decir, será el SGA el que discrimine determinados pedidos que serán gestionados por la máquina y otros no, además de recibir los datos desde el software de control del transelevador para mantener su base de datos actualizada en tiempo real.
- Los transelevadores de cargas pesadas no sólo sirven para palés: aunque el palé es la unidad de carga más común, también pueden trabajar con jaulas, contenedores o con cualquier unidad de carga de dimensiones predeterminadas.
- ¿Las unidades de carga deben ser todas iguales? No necesariamente, lo que sí es importante es que varíen poco. Las medidas de la base de la unidad de carga deben ser siempre las mismas, podremos variar en alturas, pero no sería aconsejable tener más de dos o tres alturas diferentes de unidad de carga.
- ¿Pueden combinarse con otro tipo de instalacion? Desde luego, los transelevadores de hecho, aumentan su rendimiento cuando somos capaces de combinarlos con otras instalaciones como puestos de picking, estanterías dinámicas, compactas con shuttle, etc.
- ¿Requieren mucho mantenimiento? Depende del fabricante que será el único capaz de dar este servicio y conoce su frecuencia. El coste anual mínimo está perfectamente estipulado y es conocido. Lo más importante es averiguar el coste de dicho mantenimiento y sobre todo el plazo de entrega que el fabricante maneja en piezas clave, es decir, aquellas que, en caso de avería, podrían paralizar la instalación. Y es importante saber cuánto cuestan, sobre todo en el caso de que el fabricante nos sugiera tenerlas en nuestro stock.
- ¿Cuántos palés por hora es capaz de mover? De nuevo depende y debemos acudir al fabricante. No obstante, somos nosotros los que debemos tener claro previamente el rendimiento esperado de la instalación y después comparar con lo que ofrecen las distintas marcas.
A lo largo del tiempo los transelevadores han ido evolucionando con el fin de adaptarse y dar respuesta a diversas necesidades logísticas. En este contexto, exploraremos distintos tipos de transelevadores, descubriendo algunas de sus soluciones para la optimización de los procesos logísticos y la gestión inteligente de nuestros inventarios.
Tipos de transelevadores.
Según diferentes criterios de clasificación, podemos diferenciar:
- Según el tipo de carga que manejan:
- Para cajas: también conocidos como miniload, suelen ser de dimensiones menores que sus homólogos para palés y lógicamente soportan menos peso. Están diseñados para trabajar con contenedores reutilizables de poco tamaño o cajas.
- Para palés: son máquinas de mayor tamaño y soportan mayores cargas. Están diseñados para manejar cargas paletizadas, contenedores, jaulas etc. que tengan dimensiones superiores a las que maneja un miniload.
- Según el grado de automatización.
- Automáticos: es decir, que funcionan sin la intervención de un operador humano. Están controlados por su propio software de gestión encargado de controlar todos sus movimientos y acciones.
- Semiautomáticos: que requieren la intervención de un operador humano para algunas tareas.
- Según el grado de necesidad de un operario.
- Con operario a bordo: permiten que un operario realice tareas de picking directamente desde el transelevador. Pueden estar conducidos por el operario o por el software del sistema, limitándose el operario en este caso, a indicar el momento en que cada extracción está finalizada y se puede desplazar a la siguiente ubicación.
- Sin operario: los sistemas clásicos que se dedican a ubicar y extraer unidades de carga completas, desde y hacia la cabecera, en modo automático y sin conductor.
- Según su estructura.
- Columna o mástil simple: como su propio nombre indica se trata de aquellos transelevadores compuestos por una única columna vertical. Tienen un consumo energético menor que los de columna doble.
- Columna o mástil doble: son los transelevadores con dos columnas verticales, son más estables y están preparados para manejar cargas más pesadas que los monocolumna.
- Según los pasillos de trabajo en los que trabaja.
- Un solo pasillo: es el funcionamiento más frecuente, un transelevador por pasillo, cada transelevador se desplaza siempre por su único pasillo de trabajo.
- Multi pasillo: un único transelevador atiende a varios pasillos de estanterías. Existen varios sistemas que permiten que un mismo transelevador dé servicio a varios pasillos lo que reduce el coste de la instalación y su complejidad. Veamos dos de esos sistemas para cambio de pasillo:
- Guías: una serie de guías arriba y abajo permiten que el transelevador abandone un pasillo y gire hasta alinearse con otro pasillo.
- Puente grúa: existe un tipo de transelevador que no toca el suelo. La instalación pende de un puente grúa que se desplaza sobre las estanterías posicionando el transelevador en el pasillo que se necesite. Tiene otras ventajas como que carece de cabecera y puede tomar y dejar palés directamente en el suelo en una playa, pero sacrifica la altura debido a limitaciones técnicas y al espacio que ocupa el puente grúa.
- Según la profundidad de las estanterías:
- De profundidad simple: son los más comunes y los que ofrecen un mayor rendimiento, un mismo transelevador da servicio a una estantería de profundidad simple a derecha e izquierda.
- Multi profundidad: este concepto funciona igual que para las estanterías convencionales, el transelevador está flanqueado por estanterías con dos o más palés a cada lado. En este caso la cuna del transelevador irá equipada con horquillas telescópicas o será capaz de combinarse con otros sistemas como lanzaderas solidarias, estanterías push-back o dinámicas por gravedad, que le permitan alcanzar el palé situado más profundo. Su ventaja es la mayor densidad de almacenamiento ya que necesita menos pasillos.
- Según el sistema de extracción.
- Horquillas telescópicas: son los dispositivos de manipulación de cargas más comunes. Constan de dos brazos conectados por un eje articulado, cada uno con un cuerpo fijo y varios cuerpos móviles deslizándose entre sí. Pueden trabajar a profundidades simple, doble o triple. Cuando el número de filas de estanterías supera tres, las horquillas o bien dejan de ser una solución viable o pasan a ser una solución demasiado específica y requiere muchos condicionantes, dando paso a la necesidad de sustituirlas por vehículos satélite
- Carro o vehículo satélite: en este caso las estanterías deben estar provistas de raíles a lo largo de los cuales los satélites pueden circular. El carro es transportado por el transelevador hasta la posición de almacenamiento deseada y una vez allí, es el vehículo el que lleva a cabo la acción de depositar o recoger un palé.
*Imagen de Unsplash
También te pueden interesar...
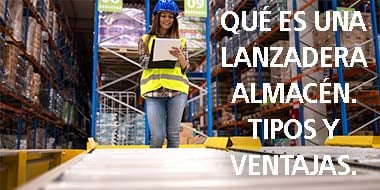
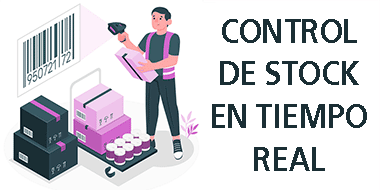