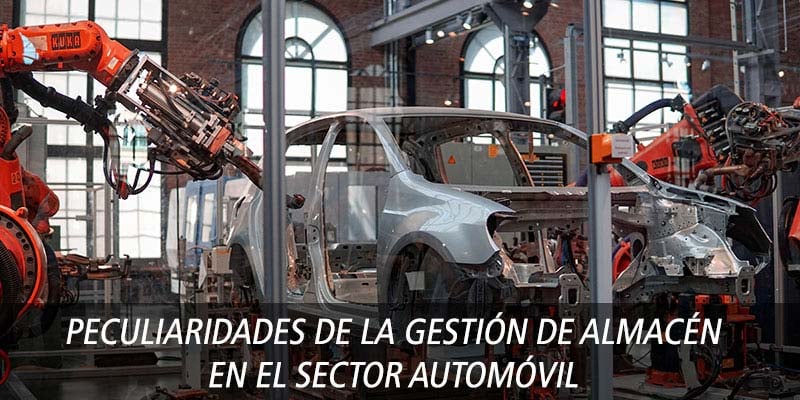
En el sector de la automoción existen tantas formas de trabajar como empresas implicadas. Nosotros en este post nos vamos a centrarnos en las particularidades de un almacén regulador que suministra piezas directamente a la cadena o línea de montaje final del vehículo, en adelante: la cadena o la línea. Veremos cómo trabaja por dentro un almacén de secuenciación de piezas para una marca fabricante de automóviles, en adelante: la marca o marca de automóvil.
Una de las primeras particularidades es que las piezas que gestiona un almacén regulador no son propiedad suya, son propiedad de la marca de automóvil. Esta particularidad tiene multitud de implicaciones, aunque en este post nos centraremos únicamente en las que más afectan a algunos de los procesos de almacenaje.
Cuando somos un almacén regulador en automoción trabajamos suministrando piezas a una cadena de montaje lo que implica que la demanda es conocida en todo momento con suficiente antelación. Pero también se trabaja contra reloj, es decir, la marca exige que realicemos todas nuestras operaciones en un período de tiempo limitado. Es la empresa del sector automovilístico la que determina el ritmo de trabajo, es la que establece los cambios (previstos o no) y es la que decide si nuestros procedimientos de actuación son los adecuados o debemos mejorarlos.
La gestión de almacén debe ser flexible, estar abierta a los cambios y adaptarse cada día a las exigencias de la línea, a las particularidades de su día a día y a sus imprevistos. Veamos algunos de los requerimientos diferenciales que afectan directamente a algunos aspectos de la gestión de almacén.
Requerimientos diferenciales en la recepción del sector del automovil
La marca de automóvil va a requerirnos que tengamos al menos un muelle de uso exclusivo con prioridad de carga y descarga para sus transportes JIT. Esto es así porque los transportes que van a llegar a nuestras instalaciones están gestionados y sincronizados por la empresa del sector automovilístico, tienen recorridos preestablecidos y asignación de tiempos concretos y muy controlados, tanto de trayecto como de carga y descarga. De esta manera la probabilidad de sufrir incidencias y retrasos es mínima y facilita un flujo constante y preciso de mercancías desde y hacia sus proveedores. Esto ayuda a mantener estables los niveles de stock en los almacenes reguladores y, en el caso de producirse incidencias o imprevistos, confiere a la marca de automóvil flexibilidad y capacidad de reacción.
Nuestro almacén debe contar con que no sólo vamos a recibir mercancías de transportes JIT de la marca por lo que tendremos que disponer, además de los muelles de uso exclusivo y privativo, los que deben ser de uso propio tanto para recepción como para expedición.
Requerimientos diferenciales de funcionamiento interno en automoción
Otra particularidad, es que la gestión de los contenedores vacíos de cada pieza requiere su propia logística. Las unidades de carga de las referencias son contenedores estandarizados de varios usos propiedad de la empresa del sector automovilístico. Esto obliga a llevar una logística paralela de todas las unidades de carga vacías que deben retornarse, repararse, limpiarse, etc. y distribuirse de nuevo para volverse a utilizar. Esto también afecta a nuestro almacén ya que necesitamos una zona delimitada para la acumulación de contenedores vacíos, hasta que la marca decida enviarnos un transporte que los retire.
El picking de piezas secuenciadas también cuenta con sus propios requerimientos diferenciales. “Secuenciadas” quiere decir que cada pieza debe suministrarse a la línea en un orden concreto, el picker debe colocar cada pieza que toma en un transporte que permita la disposición ordenada de esa pieza y de las siguientes. Un ejemplo de esos transportes son los carros divididos en celdas numeradas. La numeración de cada celda sirve para que el picker sepa en qué posición debe dejar cada referencia en las celdas: la pieza que primero coge, la depositará en la celda número uno, la siguiente en la dos y así sucesivamente. Ese orden concreto coincide exactamente con el orden que llevan los vehículos a los que las piezas deben ser incorporadas. Para una mejor trazabilidad, en el picking, cada una de las piezas queda también vinculada con el número de secuencia del vehículo en el que va a montarse, que para simplificar diremos que actuaría como su DNI y que corresponde con un número de orden en la cadena. Así la pieza colocada en la celda número uno de nuestro carro puede corresponder al vehículo con número de secuencia 124, es decir, al vehículo de la posición 124 en la cadena.
De esta manera, cuando el carro lleno de piezas (en este caso una por celda) llega a su punto de uso en la línea de montaje de vehículos, la pieza de la celda número uno, es exactamente la que debe colocarse en el vehículo que en ese momento pasa por ese punto (el 124).
Esta forma de trabajar en el punto de uso afecta directamente a la estructuración de la zona de picking del almacén regulador. Siguiendo el ejemplo anterior, la zona de picking dentro del almacén dispondrá de espacio suficiente para albergar al menos una ubicación para todas y cada una de las posibles variaciones de la pieza que debe secuenciar. Es decir, si la pieza tiene varios colores, la zona de picking deberá contar al menos con una ubicación de picking para cada color.
Evidentemente la cruda realidad no es tan sencilla como el ejemplo. La realidad es que cada punto de uso en la cadena se puede abastecer de varios almacenes reguladores, cada uno de ellos secuenciando una o varias piezas en la misma zona de picking o en varias a la vez y además cada una de las piezas tiene infinidad de variaciones que dependen no sólo del color sino del tipo de vehículo (en una misma línea pueden montarse más de un modelo de vehículo), el destino del vehículo (conductor a la derecha o la izquierda hacen variar muchas piezas), la gama, etc.
Requerimientos diferenciales del software en automoción
Una gestión tan precisa y compleja necesita de un software que esté a la altura y en niveles máximos de eficacia y eficiencia en la gestión de recursos. Además, debe estar preparado para tratar particularidades propias del sector del automóvil.
Una de las más importantes quizá sea que el software de gestión de almacén debe estar preparado para seleccionar las piezas que deben secuenciarse o suministrarse desde nuestro almacén y descartar el resto. Es decir, la marca automovilística no lanza un pedido de piezas al uso, uno a cada almacén, como ocurre en otros sectores. En automoción, en el momento se decide el mix a fabricar y se secuencia, la marca de automóvil lanza la explosión total de piezas que componen cada vehículo a todos sus proveedores. Es misión del software de cada proveedor implicado descartar todas aquellas piezas que no le corresponde tratar y seleccionar las que sí. Luego el software debe enviar, respetando la secuencia, a cada célula de montaje, producción o picking de su empresa, las órdenes correspondientes para que cada célula suministre la pieza o las piezas que le corresponden en el orden preciso.
Otra particularidad es que la marca necesita conocer exactamente y de forma fiable y regular el nivel de stock exacto que tenemos de sus referencias. Para obtener dicha información, nos obligará a realizar recuentos periódicos ciegos. Aparte de que estos recuentos cíclicos deben hacerse en un plazo de tiempo limitado, la particularidad más destacada reside en que dichos recuentos se realizarán a partir de un número concreto de secuencia que determina la marca automovilística.
Si no queremos vernos abocados a realizar estos recuentos a mano empleando mucho tiempo y recursos, nuestro software debe estar preparado para saber exactamente dónde se encuentra cada referencia implicada en el recuento (pueden ser varias a la vez) y a qué número de secuencia corresponde. Eso implica que el rastreo debe alcanzar incluso a las piezas que aún están en los carros, en los pulmones propios o de la marca, en todos los puntos de uso y por supuesto a las que están dentro de nuestro almacén. Es un recuento de cierta complejidad que además se ve agravado con penalizaciones si hay discrepancias a la baja entre el nivel de stock teórico que la marca automovilística considera correcto y el real que resulta de nuestro conteo.
Conclusión
Un sector como la automoción requiere almacenes con robustos procedimientos de actuación, supervisión constante de los mismos, mejora continua, controles de calidad muy exigentes y precisión en el desempeño de cada tarea.
Es un sector, logísticamente hablando, muy exigente, pero al mismo tiempo muy estandarizado y procedimentado lo que facilita la previsión del trabajo y nos protege de la improvisación y los imprevistos. Los almacenes de las diferentes empresas que proveen directamente a la marca principal de lo necesario para fabricar automóviles, deben entrar en un ciclo constante de mejora continua y supervisión constante de la calidad de sus productos y de la robustez de sus procesos.
En un entorno tan exigente donde el despilfarro de recursos no forma parte de la ecuación, donde todo está medido y estandarizado y donde los errores se pagan caro, es donde un software de gestión de almacén resulta especialmente útil porque busca lograr exactamente los mismos objetivos: estandarización, ahorro de recursos y reducción drástica de errores.
No olvidemos que la automoción es como la primera división logística, un sector al que no puede acceder cualquiera y cuyo funcionamiento y exigencias determinarán la estructura interna y externa de nuestro almacén. Muelles con prioridad de carga y descarga siempre disponibles, transportes específicos estandarizados y aprobados por la marca de automóvil para poder acceder a sus instalaciones, zonas de picking configuradas según las necesidades del punto de uso destino de la secuenciación de piezas, softwares con personalizaciones específicas y todo ello sin desatender las funciones propias de todo almacén, es decir, recepción, comprobación, ubicación, reposición, crossdocking y expedición.
También te pueden interesar...