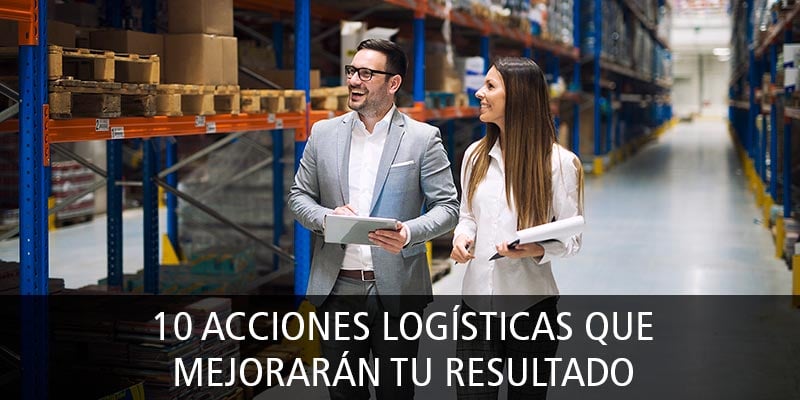
*
Siempre que hablamos de mejorar nuestros resultados, hablamos indefectiblemente de mejora en la calidad del producto o servicio que ofrecemos. Las acciones de mejora tienen siempre un doble efecto beneficioso, mejoran nuestro proceso interno y aumentan la percepción de la calidad que el cliente tiene de nuestra marca, compañía o producto. Es decir, la mejora continua de nuestros procesos implica por sí, mantener un gran enfoque en el cliente y repercute positivamente en su satisfacción, aunque no se realicen acciones que le afecten de forma directa.
Digamos que la satisfacción del cliente es consecuencia inevitable de la mejora continua de cada proceso o aspecto de nuestra compañía.
Sin embargo, mantener un nivel de servicio elevado a la vez que se optimizan los costes no es una tarea fácil ni rápida. Las acciones logísticas que podemos abordar en cada caso dependen del tipo de sector industrial al que nos dediquemos y de una gran variedad de casuísticas particulares de cada empresa, lo que constituye de facto, que la mejora continua implique un “traje a medida” para cada situación particular.
Aun así, existen problemas que mantienen una curiosa persistencia dentro de nuestras operaciones logísticas y que, salvando las distancias, admiten que podamos exponer una cierta línea de actuación válida para una cantidad de casos aceptable.
Veamos algunas acciones logísticas que podemos emprender en los campos del aprovisionamiento, almacenamiento y transporte.
Acciones logísticas de mejora en el aprovisionamiento.
Que básicamente se concretarían en aquellas acciones que nos permitan decidir con eficacia cuándo, cómo, cuánto y desde dónde reaprovisionar. Indisolublemente unidas todas ellas con la gestión de stocks y con influencia directa en sus niveles tanto para bien, como para mal, ya que se trata de reponer constante y continuamente estos stocks.
- Reponer con eficiencia. Obtendremos mejoras de rendimiento cuantos menos costes en recursos debamos asociar a esta actividad, por ejemplo, manteniendo el máximo nivel de servicio al cliente interno (por ejemplo, a producción) con las mínimas existencias posibles, lo que implicaría de entrada una menor inversión financiera tanto en adquisición como en tenencia.
- Evaluar y seleccionar. Evaluar a los proveedores ya existentes en base a criterios objetivos y seleccionar nuevos aplicando los mismos criterios. De qué sirve trabajar con proveedores que incumplen nuestros mínimos de calidad de servicio, si las consecuencias las pagaremos inevitablemente nosotros, nunca los causantes (ellos). Plazos de entrega, fiabilidad en cantidades y calidades, integridad de la mercancía, cumplimiento de fechas y horarios, son aspectos que son responsabilidad del proveedor pero que repercuten directamente sobre nuestros costes, por tanto, optimizar nuestra cartera de proveedores tendrá una repercusión directa en nuestros resultados. No todo es una cuestión de precio.
- El siguiente paso natural tras la evaluación del proveedor es caminar hacia la integración total en nuestra gestión logística. VMI (Vendor Inventory Management) o gestión del inventario por parte del vendedor implica la visibilidad total de nuestra cadena y una relación de confianza y crecimiento mutuos, además de la implantación de un buen software. Esto implica admitir algo tan inusual como completamente lógico por otra parte: que el proveedor conoce mejor sus plazos, sus tiempos de manufactura, sus transportes, etc., en definitiva, que está en mejor posición para reabastecernos que nosotros mismos, siempre y cuando tenga acceso total a toda la información necesaria para poder cumplir con nuestras necesidades. Dentro de las acciones logísticas que podemos emprender, VMI es una de las que más trabajo requiere pero que mejores resultados estables a largo plazo obtiene.
Acciones logísticas de mejora en el almacenamiento.
Tiempo, recorrido, manipulación, proceso: los cuatro jinetes del apocalipsis en un almacén. Cuanto más los simplifiquemos, reduzcamos o directamente eliminemos, obtendremos mejores resultados.
- Organización por ABC. No importa les veces que insistamos en ello, nunca deja de ser una de las formas de optimizar la gestión integral de nuestros stocks. Tanto si trabajamos dentro de un almacén dotado con grandes recursos tecnológicos como si no, el cálculo del ABC por rotación nos permitirá determinar qué recursos y procesos de control asignamos a cada tramo de producto. No debemos asignar los mismos recursos, posición en nuestro stock, ubicaciones, recuentos e incluso recursos de aprovisionamiento a un grupo de productos A que a una serie de productos C.
- Creación y uso de KPI. La forma más efectiva de reducir tiempos, acortar recorridos, manipular solo lo imprescindible y optimizar procesos dentro del almacén es estar informado y para ello es necesario medirlos. Determinar los puntos de control básicos o críticos y decidir qué indicadores del desempeño deben arrojar luz, para obtener una visión real de lo que sucede en el almacén, es la forma más efectiva de mejorar nuestros resultados. Dónde tenemos despilfarros, cuellos de botella y en qué orden abordar cada problema, es algo que podremos determinar con precisión gracias a los KPIs.
El primer paso para mejorar es saber exactamente dónde y cómo nos encontramos, realizar un diagnóstico, planificar un objetivo, ejecutar acciones, observar el resultado y medirlo con KPIs adecuados, mantener lo que funciona y volver a empezar todo el proceso para seguir mejorando lo que no.
“Sin indicadores estamos ciegos”
La intuición, la experiencia, el “buen ojo” y todas las expresiones que queramos utilizar para no usar nunca indicadores del desempeño, evidentemente ayudan, pero son como el bastón de un invidente: evitan la mayoría de los obstáculos, pero siempre habrá un andamio, un estante, una rama, que el bastón no es capaz de detectar y que, en cuestión de tiempo, acabará por traer consecuencias que tendrán mayor o menor gravedad, pero nunca deseables. Además, al seguir careciendo de indicadores (de visión), difícilmente podremos actuar para resolver el problema de raíz, por lo que parcheamos, dejando así abierta la posibilidad de que el suceso vuelva a repetirse.
- Coste de almacenamiento. Almacenar tiene un coste. Podemos medirlo o no, podemos conocerlo o no, podemos admitirlo o no, pero igualmente tiene un coste. Si tuviésemos que alquilar nuestro espacio de almacén a un tercero, seguro que no lo haríamos gratis, ni en metros cúbicos, ni en tiempo, ni en número de palés, sin embargo, cuando se trata de averiguar cuánto nos cuesta almacenar nuestras propias existencias, todos estos costes parecen diluirse y perder importancia.
“Mejorar el resultado económico en la gestión de stocks
no es siempre una cuestión de cronómetro”
- Logística inversa. Un producto que ha salido de nuestras instalaciones y viene de vuelta, ha soportado costes de aprovisionamiento, de almacenamiento, de mantenimiento, manipulación, acondicionamiento, expedición, administración, transportes y, sin embargo, al ser abonado, resulta que, como empresa, hemos asumido una cantidad ingente de costes sin beneficio alguno y no digamos si además vuelve deteriorado.
Averiguar y tipificar las causas que motivan o generan devoluciones tanto si estamos en ecommerce como si no, es el primer paso para tratar de evitarlas o reducirlas al máximo posible. Mejorar nuestra eficacia y calidad de servicio, es un principio, pero no es lo único que está en nuestra mano
Toda la cadena de suministro tiene su parte de causa de una devolución y tras una medición exhaustiva, debemos atacar en todos aquellos puntos que se desvelen como causa raíz del problema.
- Sistema SGA. Tanto la clasificación ABC por diversos criterios, como la creación y uso de los KPI, como la gestión de los recursos, la información necesaria para controlar el coste de almacenamiento, la intralogística o la optimización de la logística inversa, sus causas y opciones de mejora, se controlan en tiempo real gracias al sistema SGA.
Es la primera y más importante elección para un almacén no digitalizado ya que a partir de entonces su forma de desempeñar la actividad, su eficiencia y eficacia y sus opciones de futuro vendrán en gran medida condicionadas por las características del partner que lo suministra y del propio software.
Acciones logísticas de mejora en el transporte.
- Concentración de entregas. Podemos plantearnos ofrecer, a ciertos clientes de importancia, la posibilidad de ofertas especiales por recibir todos sus pedidos en fechas concretas sugeridas por nosotros y además siempre que sea posible, en grandes bultos consolidados, por ejemplo, paletizado. El objetivo es mejorar el resultado al reducir los costes por dos vías: por un lado, el coste de enviar un bulto grande es inferior al de enviar muchos pequeños y por otro, reducimos y concentramos el número de envíos, con lo que nuestra gestión interna y sus costes también se verán beneficiados.
- Crear valijas. Esta medida no es realizable en todos los casos. Debemos detectar qué clientes tienen mucha regularidad en la entrega de sus pedidos y no necesariamente de volumen. Por ejemplo, clientes de entrega diaria y de cantidades pequeñas. En estos casos, podemos mejorar el resultado de la gestión del transporte unificándolos, creando valijas. Optimizamos la entrega y la ruta en base a la creación de rutinas que abaraten el coste a través de la mejora de la gestión de los recursos. Eliminamos gran parte de la variabilidad del proceso si lo comparamos con la forma de trabajar sin valija.
Conclusiones
Una compañía puede ofrecer productos y servicios de calidad o no ofrecerlos. Es difícil establecer una escala de grises a este respecto, sobre todo porque no la hay. Por desgracia para nosotros mismos forma parte de nuestra cultura asumir constantemente estas escalas de tonos en gris que lo relativizan todo, pero esto, aparte de ser una actitud autojustificativa de ineficacias, es una quimera.
“La escala de grises en calidad no existe, por una sencilla razón:
porque el cliente no la maneja”
O entregamos a tiempo y en el lugar indicado o no, o buscamos la excelencia o no, o respetamos nuestros horarios de paso publicados o no, o cumplimos las expectativas del cliente o no lo hacemos, cumplimos con nuestro nivel de servicio o no, ofrecemos calidad o no la ofrecemos. Y cada vez más, las consecuencias que el cliente aplica a las empresas con incumplimientos de calidad percibida son igual de tajantes.
“Comete un error y te abandono”
Por lo tanto, la primera acción que toda compañía debería emprender, para mejorar sus resultados logísticos, no es una acción que pertenezca estrictamente al ámbito logístico. Esa primera acción debería ser admitir con humildad su situación actual. Asumir, sin tapujos ni adornos, dónde está realmente para poder marcar el camino hacia el que quiere ir y, sobre todo, para saber si lo está consiguiendo y en qué medida.
Este es el principio del camino hacia la mejora continua, de resultados o de lo que nos propongamos como compañía.
“La mejora en los resultados será la consecuencia inevitable de la aplicación de medidas de mejora continua en cualquier ámbito de actuación”
La gran dificultad con la que nos vamos a encontrar es el cambio cultural que ello implica. La mejora continua no es un cartel publicitario, no es aplicar herramientas aprendidas durante un tiempo, no es mejorar sin coordinación algunos aspectos de nuestra empresa, no es eso. La mejora continua implica un cambio cultural real en nuestra organización, es decir, que implica que de verdad se crea en ella o tiende directamente al fracaso. Esta es la gran dificultad. “La escala de grises no existe”, no es una frase hecha, es el principio del cambio cultural, el primer paso ineludible y que lo inicia todo.
“O creemos en ello y lo logramos, o no”
Algo tan simple como complejo a la vez.
*Foto de Negocios creado por aleksandarlittlewolf - www.freepik.es
También te pueden interesar...