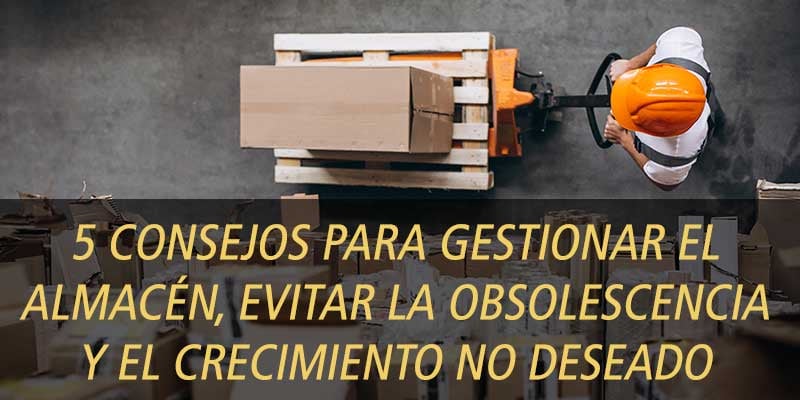
Mantener los niveles óptimos de inventario es uno de los principales quebraderos de cabeza para la gestión de almacén de cualquier empresa. Si bien es cierto, que es gracias a nuestros stocks, podemos satisfacer la demanda cuando se produce tratando de cumplir nuestro compromiso de servicio al cliente, también es cierto que el inventario requiere una inversión de capital que lógicamente no está disponible para otros usos que también son de gran interés. El problema es que la inversión en stock no suele producirse por una decisión expresa de dedicar más recursos, sino una consecuencia de múltiples factores relacionados, lo que supone detraer recursos financieros para financiar el almacén sin una decisión consciente en tal sentido. Por esto es tan importante gestionar el almacén.
La ausencia de un software para gestionar el almacén suele ser uno de los motivos del aumento excesivo de nuestros inventarios. En cualquier empresa, lo que no se mide no existe, por lo que la consecuencia de la falta de control de un sistema de gestión de almacén desprovista de herramientas de apoyo informático suele dificultar la valoración a tiempo de situaciones no deseadas relacionadas con el nivel de stock. Gestionar el almacén para ajustar los niveles de stock a las cantidades óptimas sin la tecnología adecuada es poco menos que un sueño.
Además, la falta de control de los niveles de stock provoca inevitablemente decisiones sobreprotectoras, ya que el riesgo de romper el stock se traducen siempre en excesos de inventarios. En muchos casos, tratamos los almacenes como escudos que deben protegernos de subidas de precios, desabastecimientos, variaciones en la demanda, etc.
Por último, dado que ningún producto vive para siempre, cuanto llega el cambio de tendencia o el fin de una estacionalidad, podemos encontrarnos con nuestros stocks tan saturados, que al hacer inventario parece más bien que estemos todavía al principio de temporada en lugar de al final de ésta. Todo el exceso de este producto terminado, stocks intermedios, materias primas o componentes se pueden transformar sin que nos demos cuenta (normalmente esto ocurre cuando tenemos problemas de espacio en el almacén) en un problema mayor: el temido stock de obsolescencia.
Veamos cómo actúan por separado los factores más importantes que trae consigo la falta de tecnología necesaria para gestionar el almacén y que redundarán siempre en excesos de inventario con un alto riesgo de que terminen en convertirse en stock obsoleto.
5 factores que afectan al tamaño del almacén
Entre los factores más importantes para gestionar el almacén, hay algunos que tienen una relación estrecha con el uso de herramientas tecnológicas eficientes. Podemos considerar:
1.- Compras
El desconocimiento de los niveles reales de stock actual, de los niveles óptimos de stock a mantener o de las consecuencias reales sobre el espacio, los costes y los riesgos de una saturación del mismo, además del miedo al desabastecimiento y sus consecuencias, provocan con frecuencia, adquisiciones desmedidas de materias primas y componentes, con las que el departamento trata de protegerse de la responsabilidad de un paro por desabastecimiento de la línea de producción, por ejemplo. Otras veces el sobre stock aparece por el exceso de celo a la hora aprovechar alguna oferta o por el hecho poco aconsejable de dejarse llevar por la presión de comercial o producción para que mantengamos un stock constante y abundantes de determinadas referencias.
Gracias a un software de apoyo a la gestión, podemos corregir el exceso de compras sin incurrir en riesgos no deseados, a través de una gestión colaborativa que supone una integración total de nuestros proveedores en nuestra cadena de suministros. Esto presenta multitud de ventajas, ya que podremos valorarlos adecuadamente con criterios objetivos, podremos responsabilizarles del cumplimiento de nuestros calendarios de abastecimiento y de las soluciones a problemas puntuales que puedan surgir, podremos negociar las devoluciones, acortar plazos, recibir lotes con mayor frecuencia pero de menor tamaño y ganar por tanto flexibilidad y, en consecuencia, reducir nuestros stocks a la par que los hacemos más productivos. Y todo sin sufrir un sobrecoste.
2.- Trabajar en diferido, o lo que es lo mismo, trabajar con información no actualizada en el momento de uso.
El flujo de información debe ser totalmente fiable y debe transmitirse en tiempo real, de lo contrario, la falta de inmediatez, se puede traducir en un aumento de los niveles de nuestros stocks.
Si el stock de producto terminado no se informa en tiempo real, producción no será capaz de ver sus propios progresos y es posible que produzca referencias que existen en almacén en cantidad suficiente pero que nadie es capaz de ver porque el sistema no está debidamente informado y no siempre hay tiempo para consultas que también requieren un tiempo de respuesta excesivo debido a la falta de medios. Al mismo tiempo, comercial no tramitará pedidos de dichos productos terminados por la misma razón, sencillamente cree que no están y perderá oportunidades. Además, es posible que la materia prima que ha consumido producción se descuente antes de que se den de alta las existencias de producto terminado, por lo que compras, en ese lapso de tiempo verá que la materia prima para producir no está (recordemos que no sabe aún que hay producción terminada) y tratará de reponerla. El mismo proceso afecta a los semielaborados y componentes. Ante la duda, todos los almacenes intermedios serán provistos de existencias de sobra para evitar el riesgo de las paradas de producción. Cuando la información se actualice, tendremos excesos de stock a todos los niveles y estos excesos están en riesgo de obsolescencia.
La falta de conocimiento exacto y preciso de nuestro almacén inevitablemente provoca que éste crezca sin ningún tipo de control ni criterio estratégico o de costes, ya que su crecimiento sólo atiende al criterio de “evitar males mayores”.
3.- Grandes diferencias entre el flujo de entradas y el de salidas
Si nuestros lotes de producción de producto terminado son demasiado grandes en comparación con el lote mínimo de venta y su frecuencia (si fabricamos de 100 en 100 pero vendemos de 1 en 1 cada 7 días) inevitablemente tendremos un aumento de los niveles de stock y alto riesgo de obsolescencia de todas las referencias en donde se dé esta circunstancia. Ajustar los flujos de entrada y salida de un almacén es fundamental para evitarlo. Reducir en lo posible los lotes de fabricación nos permitirá ganar flexibilidad lo que redundará en una mejor adaptación a los cambios de tendencia del mercado, solventar en menor tiempo imprevistos y posibles incidencias y adaptar nuestra capacidad productiva a la cantidad de demanda real de nuestros productos, sin necesidad de aumentar todos nuestros niveles de stock y manteniendo el nivel de servicio al cliente.
4.- Inexistencia de herramientas de previsión de la demanda
Si no contamos con un software de apoyo que nos ayude a realizar previsiones fiables de la demanda y no contamos con un sistema de producción flexible y adaptable, acumularemos stock para protegernos de las incertidumbres del mercado.
El uso de estos softwares combinado con la aplicación de un sistema MRP (cálculo de necesidades) ajusta los plazos y favorece la planificación de la producción sobre previsiones de ventas más realistas. Producción puede ajustar sus plazos y capacidades sin menoscabar el nivel de servicio al cliente ni acumular stocks. Apoyándonos en la información manejada por los MRP actuales podemos conseguir que nuestros proveedores tengan sus pedidos en fechas concretas y plausibles, podemos contribuir a que el departamento comercial elabore previsiones de venta realistas y que el departamento de producción tenga una planificación veraz y posible dependiendo de sus recursos. Una sincronización que sólo está a nuestro alcance gracias al uso adecuado de la tecnología.
5.- Falta de vigilancia de indicadores de almacén
La gestión de un almacén sin un sistema SGA adecuado reduce o anula completamente el control sobre ciertos indicadores de gestión que nos ayudan a reducir los niveles de inventario y evitar que vuelvan a crecer. Indicadores como el ABC por rotación, la tasa de cobertura, el stock medio, stocks máximos, mínimos y de seguridad deben gestionarse adecuadamente prestando mayor atención, en cuanto a niveles de stock y recuentos, a los productos de alta rotación sobre los de menor rotación. El cálculo de stocks máximos, mínimos, y de seguridad, nos alertan de sobre stocks o de posibles roturas antes de que éstas se produzcan dándonos tiempo a producir o comprar aquello que se necesite y a no hacerlo de aquello de lo que estemos abastecidos. Comparando estos datos con la previsión de ventas podremos tener una tasa de cobertura en plazo de tiempo que nos dirá cuántos días de stock tenemos de cada referencia, es decir, al ritmo de consumo actual ¿cuántos días podré abastecer la demanda sin producir más?
El control de estos indicadores (y de otros muchos que nos aporta un SGA) resulta imprescindible sobre todo si tenemos estacionalidad y deseamos tener niveles de stock ajustados.
Cómo reducir el riesgo de obsolescencia
En otro plano completamente distinto al logístico, pero que le afecta y resulta igualmente eficaz para combatir la obsolescencia, debemos ser conscientes del papel que juega en todo esto el diseño de producto.
El diseño industrial de producto y sus procesos también influye en el aumento innecesario de nuestros stocks y en el aumento del riesgo de obsolescencias, ya que no es lo mismo fabricar contra stock del producto terminado, que contra un producto semielaborado, común para varios productos terminados sobre el que aplicaremos un proceso de personalización final.
Por ejemplo, en la producción de muebles, la tendencia será conseguir que el diseño de productos tenga un enfoque modular, de esta forma existen una serie de elementos que configuran el tipo de mueble (básico) y otros elementos que personalizan el acabado final para el cliente.
La idea es fabricar y almacenar los elementos modulares básicos por tipo de mueble, de forma que, la personalización, que es lo que mayor riesgo tiene de sufrir obsolescencia, nunca se almacena o se almacena un corto período de tiempo, ya que, el diseño modular permite la personalización final en un tiempo muy corto contra pedido, sin alargar los plazos de servicio.
Conclusiones
Hemos visto cómo la falta de tecnología provoca consecuencias indeseadas como el exceso de compras, la pérdida de oportunidades, desincronización entre departamentos, imposibilidad de planificar, desajustes entre entradas y salidas, pérdidas de exactitud e inmediatez en la información que redunda en falta de confianza por escasez de multitud de datos y por escasa fiabilidad de los existentes. En consecuencia, o como respuesta a todo ello, inflamos nuestros stocks, bien sea por los errores provocados por ineficacias en el sistema o bien por exceso de celo protector.
Mejorar el diseño de producto contribuye definitivamente a evitar estos riesgos casi tanto como una buena gestión de la información y de las mercancías.
Un aumento de nuestros stocks sin adecuarlos a los requerimientos propios y de nuestros clientes, supone incurrir en un riesgo de obsolescencia, que además de las pérdidas asociados, ocupan un espacio que lo convertimos en improductivo durante tiempo indefinido.
*Business photo created by senivpetro - www.freepik.com
También te pueden interesar...