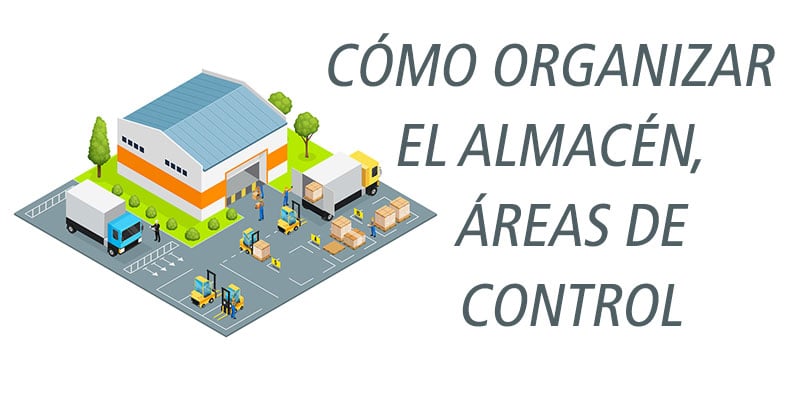
La forma en que debemos afrontar la organización de almacén consta de una serie de decisiones críticas a las que en demasiadas ocasiones prestamos poca atención. Las distintas configuraciones de los almacenes en muchas ocasiones responden a la necesidad de adaptación de la empresa a las nuevas situaciones que su desarrollo evolutivo impone, y no a un diseño meditado en el marco de la gestión de almacén. Es decir, que básicamente se va “apañando” el diseño y dimensiones del almacén como buenamente se puede, forzándolo a adaptarse a los cambios que el crecimiento empresarial impone, pero sin ningún criterio de productividad. Esta tendencia de crecimiento incontrolado y adaptativo suele prolongarse en el tiempo sin que nadie repare en ello, hasta que los problemas de liquidez, de sobre stock, de excesos de obsolescencia, de deterioro de las referencias o todos a la vez, la hacen del todo insostenible.
Pero siempre estamos a tiempo para organizar el almacén y hacerlo más productivo. Para ello es necesario que, en primer lugar, conozcamos las diferentes áreas básicas de las que se compone un almacén y definamos claramente qué necesitamos que ocurra en cada una de ellas, es decir, qué procedimientos de actuación van a desarrollarse en cada área.
Las áreas de control en un almacén
La principal premisa de organización de un almacén es tener definidas con precisión las siguientes zonas de trabajo:
ZONA DE CARGA Y DESCARGA
Estas zonas a las que suele prestarse poca atención resultan ser de vital importancia ya que constituyen el lugar por donde van a entrar y salir físicamente las mercancías y deben hacerlo de forma ágil y rápida y sin sufrir percance alguno. Lo ideal es que ambas zonas no coincidan en el mismo espacio físico, sino que estén separadas, preferiblemente en lugares opuestos del almacén. Es decir, si la zona de descarga está en el ala sur, la de carga debería situarse en el ala norte. Esta disposición pretende agilizar al máximo el flujo de mercancías logrando que éstas sigan una trayectoria lo más recta posible.
ZONA DE RECEPCIÓN O PLAYA DE ENTRADA
La zona de recepción de mercancías es aquella en la que realizaremos normalmente varios procesos: identificación de la mercancía en comparación con el albarán de transporte, control de calidad y clasificación. Si disponemos de un sistema SGA tras esos dos procesos añadiremos el de entrada al sistema y etiquetado previo a su ubicación si procede.
También es posible que posteriormente a la identificación, recepción y clasificación debamos transformar las unidades de carga recibidas en otras más adecuadas para su ubicación. En ese caso la zona debe estar equipada con lo necesario para realizar esta labor de forma segura y eficiente.
ZONA DE ALMACENAJE
Es la zona de almacenaje propiamente dicha, donde van a quedar ubicadas las mercancías. Debe aprovechar al máximo la altura de almacenaje disponible, es decir, el espacio vertical al mismo tiempo que realizamos un diseño que aproveche al máximo la superficie horizontal. También deben considerarse zona de almacenaje los almacenes intermedios y los que se ubican a pie de máquina, por ejemplo.
ZONA DE PREPARACIÓN DE PEDIDOS O PICKING
En algunos almacenes donde la unidad de carga de salida es exactamente igual a la de entrada estas zonas pueden no existir. Pero donde sí son necesarias, es decir, donde la unidad de carga de entrada no corresponde con la de salida estas zonas pueden estar integradas en la zona de almacenaje o separadas.
- Integradas
Se utiliza como zona de picking son las propias estanterías de almacenaje, es decir, los productos se desmontan de sus unidades de carga originales para incorporarse a pedidos individuales en las propias estanterías donde se ubicaron. - Separadas
Son aquellas que quedan para uso exclusivo del proceso de picking, es decir, que la zona de almacenaje y la de picking son diferentes y están separadas. Este tipo de zonas recibe reposición de mercancías desde la zona de almacenaje conforme el proceso de picking lo va requiriendo. Las unidades de carga completas se ubican en posiciones fijas en el suelo para que los operarios las vayan desmontando en función de los pedidos que deben atender. O bien la puede estar formada por estanterías especialmente diseñadas para ello con casillas o módulos de diferentes tamaños dependiendo del producto que deban albergar y que son abastecidas desde la zona de almacenaje normalmente siguiendo la política de una casilla, una referencia.
ZONA DE EXPEDICIÓN O PLAYA DE SALIDA
La zona de expedición está destinada a la agrupación y al embalaje, si procede, de los pedidos preparados y es donde se producirá la acumulación de mercancías que deben salir del almacén para cargarse en los camiones de distribución.
Debe ser contigua a la zona de carga y para agilizar los movimientos y evitar errores cada carga completa de camión debe esperar junto a su muelle.
En los casos en que el almacén esté apoyado por un SGA será en esta zona donde se informará al sistema de los pedidos concretos que van a introducirse en cada camión. En algunos casos incluso se crea la documentación necesaria de albaranado y transporte en esta zona.
Posibilidades en el diseño de tareas
Los procedimientos de actuación en cada una de las áreas de nuestro almacén variarán en función de múltiples factores como los medios de los que dispongamos, la tecnología con la que estemos equipados, la naturaleza del producto, los controles propios de cada empresa, etc. Por ello es imposible determinar un estándar común a seguir para cada zona sin embargo sí podemos detallar unas líneas generales de actuación que sirvan como base.
ZONA DE RECEPCIÓN
Por ejemplo, en esta zona será conveniente establecer la forma correcta de determinar con precisión si la mercancía esperada es la misma que la recibida y si se ha recibido en la cantidad y calidad adecuadas.
Dependiendo de la unidad de carga a recibir y de la naturaleza de los productos tendremos que establecer unos estándares de control u otros. Por ejemplo, podemos recurrir a sistemas de conteo por pesaje si vamos a recibir materia prima y componentes para una línea de fabricación cuando estos productos son de gran tonelaje o vienen a granel en gran número de unidades. Si la posibilidad del conteo existe entonces debemos procurar mantener una zona despejada que permita trabajar en dicho control con facilidad y sin interrupciones, mucho más si para ello debemos desmotar la unidad de carga del proveedor y recomponerla en unidades de carga diferentes para poderla ubicar o si debemos realizar labores de clasificación porque lo recibido viene mezclado en diferentes unidades de carga y lo que contiene en cada una de ellas no viene detallado así en el albarán.
Lo ideal por supuesto es concertar con el proveedor estándares de calidad que debe cumplir su producto no solo respecto al mismo, su número y calidad, sino también respecto a la configuración en peso y medidas de su unidad de carga y etiquetado de la misma. Estos estándares serán los de nuestro almacén. De esta manera y estando nuestro almacén equipado con un SGA el proceso de entrada se reduce a una rápida lectura de las etiquetas de las etiquetas estandarizadas en cada una de las unidades carga del proveedor. Dado que la unidad de carga es exactamente la que admite nuestro almacén y los controles de calidad recaen en el proveedor, así como las consecuencias de su no cumplimiento, no se necesitan más trámites excepto quizá algún muestreo ocasional de control.
Si además debemos recibir producto en curso de fabricación la zona de recepción de estos debe estar separada del resto y despejada. Debe estar separada en la medida de lo posible de la zona de recepción de materia prima y componentes ya que su gestión es diferente.
Los controles, de haberlos, son diferentes y el destino y la ubicación de este tipo de producto también debe ser diferente. Debe estar próxima a la línea de fabricación para evitar desplazamientos innecesarios y su zona de almacenaje debe ser adecuada para las unidades de carga de dicho producto que no necesariamente coincidirán con los del resto de productos que provengan de proveedor. En algunos casos incluso se necesitarán medios de manutención propios.
ZONA DE ALMACENAJE
Esta zona es donde se instalarán los diferentes sistemas de almacenaje que deben adaptarse a los diferentes tipos, pesos, medidas, alturas, embalajes, naturalezas, etc., de la mercancía que debe albergar. Esta zona acumula muchas decisiones críticas para la gestión de todo el almacén que son las que afectan a los flujos de referencias, de información, la creación de recorridos, alturas, elementos de manutención necesarios, etc.
Un buen criterio para la distribución de las referencias puede ser acortar al máximo los movimientos que dichas referencias deben realizar dentro del almacén. Para ello debemos conocer el lugar que ocupa cada referencia en un ABC por rotación y debemos ser conscientes que este ranking cambia con el tiempo por lo que deberemos recalcularlo con frecuencia si no disponemos de un sistema que nos lo proporcione en tiempo real como un SGA.
De esta forma las referencias de alta o muy alta rotación tanto si se trata de materia prima, componentes, producto en curso, mercaderías o producto terminado, deben ubicarse lo más cerca posible de su punto de uso, de picking o zona de expedición. De esta manera aumentamos su disponibilidad y acortamos tiempos en el momento surja la necesidad de su uso.
Por ello es conveniente tener el almacén distribuido en zonas separadas para cada tipo de referencia. No se gestiona igual la materia prima que el producto terminado ni siquiera suele coincidir el tipo de ubicación que se necesita en cada caso. Las zonas deben ser independientes de manera que las ubicaciones destinadas materia prima y componentes no se mezclen con las de producto en curso o con las de producto terminado.
De la misma forma debemos separar dos áreas que a nuestro juicio son fundamentales y en muchas ocasiones, olvidadas o ignoradas. La zona de obsolescencias y la de control de calidad. Tener espacios físicos bien delimitados para ambas lo primero que nos proporcionará será una perspectiva visual del dimensionamiento que estas referencias obsoletas o con problemas de calidad producidos por nuestra propia cadena de producción pueden llegar a alcanzar. Además de el dimensionamiento visual debemos separar ambas zonas del resto dado que la gestión de obsoletos, que en muchos casos se limita al reordenamiento y recuento continuo, nada tiene que ver con la de referencias de todo tipo que presentan defectos de calidad y que deben ser desechadas o retrabajadas.
Esto es una norma general otros factores cono el tipo de ubicación disponible, elementos de manutención, índice de ocupación, espacio, etc., pueden hacer variar estos criterios de creación de zonas dentro del almacén. Cuando estamos equipados con un SGA el software se encarga de mantener estas zonas correctamente gestionadas en todo momento.
ZONA DE PREPARACIÓN DE PEDIDOS O PICKING
En esta zona de nuevo entramos en el terreno de las decisiones personalizadas multicriterio. Existen tantos procedimientos y soluciones como empresas en el mercado.
Si debemos servir multitud de pedidos pequeños a diferentes destinos quizá debamos plantearnos un picking por oleadas, es decir, una única acción de picking para todas las referencias de todos los pedidos de manera que con un único recorrido por la zona recopilemos todas las referencias de todos esos pedidos. Lógicamente estarán mezcladas por lo que deberemos contar con una zona de consolidación donde realizar un segundo picking sobre estas referencias para conformar uno por uno todos los pedidos.
Si por el contrario nuestros pedidos son de cierta envergadura o la naturaleza de nuestro producto lo aconseja quizá nos convenga realizar una única acción de picking por cada pedido. De esta manera por cada pedido de cliente realizaremos una única acción de picking hasta completarlo. Puede darse el caso que debamos incorporar elementos personalizados que permanezcan en estado semielaborado hasta que haya demanda del cliente. En este caso, podemos tratar estos productos con sus personalizaciones en el área de semielaborados y realizar el picking y el embalado en esa zona, de manera que el producto terminado llegue al almacén totalmente listo para su expedición. Si contamos con un software de gestión las diferentes acciones pueden sincronizarse para que el producto terminado y personalizado llegue embalado directamente a la playa de salidas, para incorporarse al resto del pedido preparado justo en el momento previo a su expedición.
A continuación vamos a resumir en el siguiente cuadro algunas alternativas al diseño de los distintos procedimientos.
ÁREA DE CONTROL |
PROCESO |
ALTERNATIVAS DE DISEÑO PROCEDIMIENTO |
VENTAJAS |
INCONVENIENTES |
Carga y descarga |
Entrada y salida física de mercancías |
Adecuadas a la unidad de carga Equipadas con puertas de apertura y cierre automáticos A distinto nivel que el de circulación del camión Equipadas con sistemas de ajuste de nivel |
Agiliza la entrada y salida de transportes y mercancías |
Con falta de medios o medios inadecuados dificulta ambos procesos. |
Recepción |
Identificación, control de calidad y clasificación, etiquetaje e información al sistema si existe. |
Identificación, control de calidad, clasificación, etiquetaje, escaneado. Aprovechamiento de espacio horizontal Debe estar muy bien delimitada Debe ser una zona independiente |
Mejora el flujo de mercancías Garantiza el control de calidad Permite clasificar las referencias. Permite preparar o transformar la unidad de carga para su ubicación |
Requiere de una programación estricta de entradas. Tentador uso del espacio para ubicar otro tipo de mercancías Posibles sobrecargas de trabajo seguidas de inactividad Tiende a llenarse dificultando las labores que deben realizarse en ella. |
Almacenaje |
Ubicación, custodia y conservación de las referencias. |
Aprovechamiento del espacio en altura y de superficie Puede albergar zonas de picking Requiere SGA Disponibilidad, custodia, localización, conservación, integridad, de referencias. Ubicación por rotación Separación de zonas |
Permite almacenar el producto en perfecto estado. Debe adaptarse a la naturaleza de las referencias que debe albergar Su diseño es clave para el buen funcionamiento de los procesos previos como de los posteriores.
|
Su diseño requiere de conocimientos expertos. Gran variabilidad de opciones. Un mal diseño puede comprometer la integridad de las referencias. Sin medios tecnológicos y en almacenes de cierto tamaño la localización de referencias puede llegar a ser misión imposible. |
Preparación de pedidos |
Picking de productos |
Picking en altura, a nivel de suelo, manual, mecánico, Zonas integradas Zonas separadas Picking pedido a pedido, por oleadas o combinación de ambos. |
La satisfacción del cliente y el nivel de servicio residen casi en su totalidad en esta zona Permite adecuar las unidades de carga de entrada a las de salida. |
Sin los medios adecuados es la zona donde más tiempo se despilfarra Se producen multitud de errores Fase final requiere vigilancia o medios y ayudas técnicas. |
Expedición |
Consolidación de la carga de cada transporte |
Debe aprovechar el espacio horizontal Consolidación de pedidos |
Agiliza la carga de pedidos en el transporte Evita errores de carga Permite que los pedidos terminados esperen al transporte en una zona segura Permite embalar o filmar los pedidos |
Pueden mezclarse pedidos entre transportes si sus dimensiones no son adecuadas. Propensas a golpes y caídas de pedidos por un mal filmado o embalaje |
Conclusiones
Hemos determinado a grandes rasgos las zonas básicas que componen un almacén ya que la forma de organización de almacén afecta directamente a su gestión. Cada zona debe diseñarse de forma independiente, pero sin perder de vista la visión de conjunto. La gestión de almacén debe ser íntegra, es decir, debe diseñar cada zona, dimensionarla y ubicarla, y al mismo tiempo tratar de sincronizar las acciones que se producen en cada área, para lograr un fin común: satisfacer la demanda de nuestros clientes cada vez que se produce, justo en el momento que se produce y en el lugar que se produce.
Una vez hecho esto, indudablemente un soporte tecnológico adecuado como un sistema de gestión SGA nos ayudará conocer todos los resquicios procedimentales de nuestro almacén, todas las dimensiones espaciales y económicas de cada familia, referencia, equipo de manutención, personal, etc. Puede incluso servirnos de patrón dado que el SGA se fundamenta en patrones óptimos de actuación que podemos comparar con los procedimientos que seguimos previos a su implantación.
Organizar el almacén, si no partimos de cero, es una labor ardua que requerirá de nosotros grandes dosis de paciencia, templanza y optimismo. Hemos redactado este post porque sabemos que puede hacerse esté en el punto que esté su almacén. No debemos caer nunca en la desesperanza que supone la abrumadora comparación de nuestra situación actual con la idealizada visión del todavía lejano objetivo a conseguir. Todo grano de arena hace montaña y una vez hemos dado el primer paso, estamos un paso más cerca de conseguirlo.
*House vector created by macrovector_official - www.freepik.com
También te pueden interesar...